Abstract: To meet the requirements of large instantaneous thrust,high working and return speeds of demoulding cylinder in the hydraulic system of brick-making machines,a double-construction hydraulic speed-boosting cylinder was designed. The structural design and the setting of the main parameters of the designed cylinder were given. The strut stability was confirmed. Production results show that the demoulding speed-boosting cylinder can operate smoothly and reliably and can improve the demoulding quality and production efficiency.
Keywords: brick making machine; hydraulic cylinder; demoulding; speed-boosting cylinder
The demolding cylinder in the hydraulic system of the brick making machine requires sufficient thrust to push a large load at the moment of demolding, and the load decreases after demolding is completed. In order to improve production efficiency, it is required to have a larger working speed (>260 mm/s) and a larger return speed (>430 mm/s). If an ordinary single rod piston cylinder is used, in order to generate large thrust, the effective working area of the rod free piston in the hydraulic cylinder should be large enough. In the case of a large working area, according to the velocity formula V=Q/A, the working speed V is not necessarily very large, so ordinary single rod piston cylinders cannot meet its requirements.
In order to meet the working requirements of the demolding cylinder in the hydraulic system of the brick making machine, a seed mother type hydraulic speed increasing cylinder is designed for use in the hydraulic system of the brick making machine. The article elaborates on the design process of the speed increasing cylinder, including the structural design of the speed increasing cylinder, determination of main parameters, stability calculation of the pressure rod, etc., and compares the speed of the speed increasing cylinder with ordinary single rod piston cylinder.
1. Working principle of ordinary speed increasing cylinder
At present, the speed increasing cylinder commonly used in industrial production is shown in Figure 1, which is composed of a piston cylinder and a plunger cylinder. When the pressure oil enters the small chamber 1 of the speed increasing cylinder through the plunger hole, it pushes the piston to move quickly to the right. At this time, the large chamber 2 needs to be filled with liquid, and the piston outputs less thrust. When the pressure oil enters the large chamber 2 of the speed increasing cylinder, the piston shifts to slow forward and the output thrust increases. As can be seen from the above, this type of speed increasing cylinder first generates a large speed, and then forms a large thrust. The working requirement of the demolding cylinder in the hydraulic system of the brick making machine is to have a large instantaneous thrust first, and when the load changes after demolding is completed, a larger working speed is required to improve production efficiency.
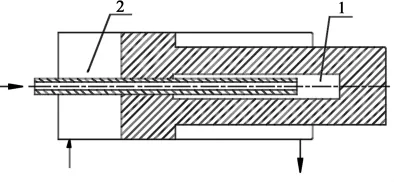
Figure 1 Structure diagram of ordinary speed increasing cylinder
2. Working conditions and requirements for demolding cylinders in the hydraulic system of brick making machines
1) The rated pressure of the system is 25 MPa, and the maximum load of the system is approximately 220 kN.
2) After the demolding is completed, a large working speed (>260 mm/s) is required, and a large return speed (>430 Mm/s).
3) The working stroke is 400 mm.
3. Structural Design of Demolding Speed Increasing Cylinder
3.1 Basic structural design of demolding speed increasing cylinder
In order to meet the requirements of the demolding cylinder in the hydraulic system of the brick making machine, which requires both large instantaneous thrust and large working speed and return speed, and to comprehensively compare the performance characteristics of various types of hydraulic cylinders, a sub mother type hydraulic speed increasing cylinder structure is designed, which is to cover a small hydraulic cylinder inside the large hydraulic cylinder, and the piston rod of the large hydraulic cylinder also serves as the cylinder barrel of the small hydraulic cylinder. The structural diagram of the designed demolding speed increasing cylinder is shown in Figure 2. In order to make the structure compact and minimize internal leakage, the large piston 4 and the large piston rod 5 are welded together to form an independent large piston rod component unit, as shown in Figure 3. During assembly, they are threaded together with the guide sleeve to form a moving component. For the same purpose, weld the oil guide tube 1, the small piston rod 6, and the connecting head together to form an independent small piston rod component unit, as shown in Figure 4.
Working principle analysis of demolding speed increasing cylinder (Figure 2): Firstly, pressure oil enters chamber A of the hydraulic cylinder from port P1. At this time, due to the large working area of chamber A, a large thrust can be obtained, achieving smooth demolding. After the demolding is completed, the actual load decreases, and the pressure oil enters the oil guide pipe through the P2 port. Through the oil guide pipe, it enters the B chamber of the hydraulic cylinder. At this time, due to the small working area of the B chamber, a larger movement speed can be obtained. The hydraulic cylinder returns with oil from the P3 port, then enters the C chamber through the gap between the small piston rod and the oil guide pipe, and then through the small hole on the small piston rod. Due to the difference of only 30 mm between the diameter D2 of the small piston and the diameter d2 of the small piston rod, the working area of the C chamber is very small, so a large return speed can be achieved.
The designed demolding speed increasing cylinder (Figure 2) has slight similarities in structure with ordinary multi-stage hydraulic cylinders, but there are significant differences between the two. Firstly, their application scenarios are different. Multistage hydraulic cylinders are generally used in situations where the installation position is limited and the stroke requirement is long, while the designed demolding speed increasing cylinder should be used in situations where high instantaneous thrust and high working speed are required; The second reason is that their movement during operation is also different. When a multi-stage hydraulic cylinder is in operation, the pistons at all levels act in order of their effective action area. When extending, the larger action area moves first, the smaller action area moves later, and when retracting, the action sequence is opposite [1]. However, when the demolding and increasing speed cylinder shown in Figure 2 is in operation, only the larger cylinder acts, while the smaller cylinder is fixed, which greatly enhances its compression stability and working stability, This is particularly important in high-pressure situations.

1. Oil guide pipe 2. Guide sleeve for small piston rod 3. Cylinder barrel
4. Large piston 5. Large piston rod 6. Small piston rod 7. Small piston
Figure 2 Structure diagram of demolding speed increasing cylinder
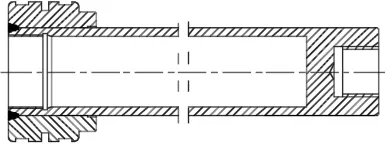
Figure 3 Large piston rod assembly

Figure 4 Small piston rod assembly
3.2 Sealing Structure Design of Demolding Speed Increasing Cylinder
Due to the working pressure of the system being 25 MPa and the pressure resistance of the hydraulic cylinder reaching 31.5 MPa, it belongs to the high-pressure category, and also requires a large working speed and return speed. Therefore, the application environment of this demolding speed increase cylinder belongs to the high-speed and high-pressure category. Under such working conditions, how to correctly select the sealing structure, especially the dynamic sealing structure, is the key to the structural design of this booster cylinder. The commonly used seals for hydraulic cylinders mainly include O-ring seals, Y-shaped seals, U-shaped seals, V-shaped composite seals, sliding ring composite seals, etc. The pressure resistance of each seal is different, and their application scenarios are also different. When designing hydraulic cylinders, the choice of sealing form is not a simple call for commonly used sealing components mentioned above, but an optimized combination of sealing forms based on specific conditions such as working pressure, working conditions, and movement speed of the hydraulic cylinder, such as O-ring and Y-shaped sealing ring, U-shaped ring and U-shaped ring, U-shaped ring and sliding ring combination sealing ring, etc. In high-pressure and high-speed hydraulic cylinders, piston seals are commonly used with grid rings, and rod seals are commonly used with U-ring Gaster seals. Taking into account the performance characteristics of various types of seals and the application environment of this demolding speed increasing cylinder, the sealing structure of the large piston and cylinder barrel adopts a sliding ring combination seal (grid ring) with holes, as shown in Figure 5. The two support rings are used for bearing and guiding. The sealing structure of the small piston rod and guide sleeve adopts a combination of U-shaped rings and shaft sliding ring type seals (ST seals), as shown in Figure 6. Due to the bidirectional load borne by the guide sleeve, the opening direction of the seals should also be towards both sides, which should be paid special attention to during the assembly of hydraulic cylinders. Due to the high pressure and harsh working conditions, the sliding ring combination seal still has very high pressure stability, good thermal conductivity, good extrusion resistance, high wear resistance, low friction, and other performance. When applied in this hydraulic cylinder, it can ensure no leakage and achieve rapid goals.
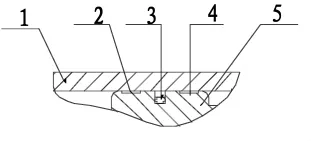
1. Cylinder barrel 2. Support ring 3. Sliding ring combination seal for holes
4. Support ring 5. Large piston
Figure 5 Sealing structure between the large piston and cylinder barrel
4. epilogue
The sub mother type hydraulic speed increasing cylinder of this design was designed based on its thrust requirements, considering factors such as strength requirements, standard series of piston rods and cylinder barrels, and manufacturing process of hydraulic cylinders. Its structure and main dimensions were designed, and the stability of the pressure rod was checked. By comparing the speed of the demolding speed increasing cylinder with that of the ordinary hydraulic cylinder, it can be seen that the working speed of the demolding speed increasing cylinder after demolding is 3.6 times that of the ordinary hydraulic cylinder, and the return speed is 4 times that of the ordinary hydraulic cylinder.
The designed demolding speed increasing cylinder has been running in the hydraulic system of the brick making machine for over a year, and it works smoothly and reliably during operation, greatly improving work efficiency.