Abstract: This article introduces the production process of HQY-100E hydraulic brick making machine, summarizes the common quality problems in the production of colored cement concrete pavement bricks by this equipment, and proposes specific prevention and control measures, which can serve as a reference for some peer units.
Keywords: cement concrete pavement bricks; Brick making machine; Batching system; Microcomputer control
With the rapid development of China’s economy and the demand for urban construction and environmental beautification, colored pavement bricks are increasingly favored by people due to their diverse and unique charm. Colored road tiles, also known as pedestrian tiles, are mainly used for environmental beautification of sidewalks, squares, courtyards, and residential areas, as well as for parking lots and roadways. It can design unique and pleasing colored roads through the combination of its plate shape and color, while also possessing high compressive strength, wear resistance, good freeze-thaw resistance, and durability. Its anti slip effect and construction technology are superior to conventional large block pavement bricks. In order to accelerate the construction of small towns and beautify the environment, the state-owned Huaihai Farm in Jiangsu Province purchased a HQY-100E hydraulic brick making machine from Shanghai Zhongyin Electronic and Mechanical Engineering Company in early 1997. The production process is shown in Figure 1. The colored cement concrete pavement bricks produced by this process have advantages such as high strength and density, good wear resistance, and good surface sliding resistance. In several years of production practice, common quality problems and prevention measures that are prone to occur in the production of colored cement concrete pavement bricks using this equipment have been summarized. Based on the actual situation, the summary is as follows:
1. Surface pores (surface adhesion)
1.1 Phenomenon and Cause Analysis
This phenomenon occurs during the molding process, manifested as small holes formed on the surface of the brick body due to individual particles adhering to the pressure head when the brick is transported out from the pallet ‚ Affects appearance quality. According to the industry standard concrete pavement bricks (JG446-91), if the area of holes formed by adhesive skin is greater than 5 square centimeters, it is considered unqualified. The cause of this phenomenon is due to material quality issues, which are caused by the moisture and clumping of mud or cement in the fabric sand, which cannot be dispersed.
1.2 Prevention and control measures
1.2.1 Strictly control the quality of raw materials (sand) and cement, and do not use unqualified raw materials.
1.2.2 Sieve the sand used for the fabric (water sieving is the best) to remove mud and coarse particles.
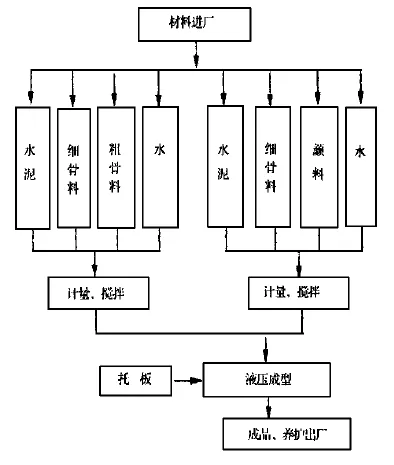
Figure 1 Production Process Flow of HQY-100E Hydraulic Brick Making Machine
1.2.3 If using a cement tank, attention should be paid to the sealing performance of the cement tank, and moisture-proof measures should be taken for the cement stacking area. Cement that has exceeded its service life and has agglomerated must be discarded.
1.2.4 Increase the concrete mixing time appropriately.
2. Crack
2.1 Phenomenon and Cause Analysis
There are several reasons for the occurrence of penetrating or non penetrating cracks in cement concrete pavement bricks: ① Inappropriate production process parameters ‚ If the pressure is too strong; ② The upper and lower molds are not level, causing lateral stress to be applied to the bricks during demolding; ③ The strength of the support plate is insufficient. If small wooden boards are used to assemble the support plate for a period of time, it is easy for screws to loosen, causing the rebound stress of adjacent small wooden boards after compression to be unequal in magnitude and asynchronous in time; ④ Micro cracks caused by untimely maintenance.
2.2 Prevention and control measures
If cracks appear, attention should first be paid to observing the above aspects and analyzing which category they belong to. An accurate and effective identification method is: if the cracks are small and irregular, the first consideration is ④ maintenance factors; If the direction of most brick cracks is parallel to the splicing direction of the support plate, the strength of the support plate should be considered first; If the position of the brick with cracks is relatively fixed in the pallet, the horizontal condition of the mold should be considered first; If the reasons cannot be identified from these three aspects, consideration should be given to ① hydraulic process parameters. After identifying the corresponding main reasons, further verification can be conducted to break them down from point to face, one by one, and the problem can be easily solved. We have found the most serious problem in production, which is the third type. In response to this problem, we have implemented regular maintenance of the pallets and gradually replaced the old assembled pallets. After trial use of pallets made of different materials and optimization of performance price ratio analysis, we have used seamless high-strength fiberboard as the pallets, and the application effect is excellent. The corresponding prevention and control measures are summarized as follows:
2.2.1 Strictly control the quality of the pallet, and use high-strength, seamless fiberboard as the pallet.
2.2.2 Select appropriate process parameters for production.
2.2.3 When replacing the mold, appropriate tools should be used to ensure that the upper and lower molds are level with the base.
2.2.4 Timely watering and maintenance
3. Severe honeycomb and pitted surface on the side
3.1 Phenomenon and Cause Analysis
Severe honeycomb on the side of cement concrete pavement bricks with large and numerous voids ‚ Affects appearance and strength. The main reason for this problem is that the concrete mix proportion used for the base material is unreasonable, and adjustments should be made to the mix proportion used for the base material.
3.2 Prevention and control measures
3.2.1 Select appropriate concrete mix proportions through practical comparison, as shown in Table 1.
Note: The moisture content of sand and stone is less than 2%.

Table 1 Mix proportion of cement concrete pavement brick base material
The pavement bricks produced using the concrete mix proportion in Table 1 have a 3-day compressive strength of 35MPa, which meets the strength requirements specified in standard JC446-91.
3.2.2 Using appropriately graded raw materials for production can completely replace crushed stone and sand with stone chips. However, due to the high soil content and large changes in soil content in the particle grading of stone chips, the quality is unstable and difficult to control. When the stone chips are too thick, there will be honeycomb and pitted surface on the side, which affects the appearance quality. Therefore, using crushed stone and sand is relatively easy to control.
4. Large fluctuation in intensity
4.1 Phenomenon and Cause Analysis
The experiment found a significant difference in strength, which cannot meet the design requirements. There are many factors that can cause this problem, and it can be classified into two categories that have a significant impact: one is due to improper mechanical maintenance, and the other is material segregation. The concrete mixed by the batching system is transported through a belt and unloaded into the brick making system hopper with a certain height difference. In addition, the concrete is relatively dry, hard, and loose, which is prone to coarse and fine particle segregation. For nearly a month, our laboratory conducted a random inspection and found that the strength of the bricks fluctuated greatly. The maximum compressive strength of a single block is 39MPa, while the minimum value is only 18MPa. Through our careful analysis, it was found that the difference in thickness between the rear and front rows of the same brick produced was as high as 2mm, which is severely tilted and uneven. Further inspection revealed that the difference in compressive strength between the two rows of bricks reached 15MPa (with an average compressive strength of 40MPa in the rear row and 25MPa in the front row). Through observation and analysis of the production process, it was found that the reason was due to excessive wear and tear on the scraper plate of the hopper, resulting in uneven feeding of the hopper, This resulted in an excessive amount of bottom material being sent to the back row bricks, as well as improper handling by the operator after the aging of the front and rear shock absorbers of the brick making machine base, resulting in uneven stress during compaction. Therefore, the strength difference occurred. By adjusting these factors, the problem of strength fluctuation was solved.
4.2 Prevention and control measures
4.2.1 Equipment should be carefully maintained on a regular basis.
4.2.2 Try to reduce or eliminate the height difference during unloading to prevent concrete segregation.
4.2.3 Analyze the experimental results using statistical techniques and ensure that the production process quality is in a stable and controlled state.
4.2.4 Quality inspection personnel should promptly and carefully inspect and analyze the appearance quality such as size deviation, and provide timely feedback on quality information to the quality control department.
5. Inconsistent surface gloss of colored bricks
5.1 Phenomenon and Cause Analysis
This factor is not only due to errors in the ingredient system itself, but also due to quality issues in the pigment itself. We have purchased pigments from the same manufacturer and found differences in the color of iron oxide red pigments from different batches.
5.2 Prevention and control measures
5.2.1 Choosing a high-quality and reliable pigment manufacturer is a prerequisite for ensuring color consistency. If conditions permit, you can visit nearby pigment manufacturers for inspection and select samples for analysis ‚ Select a pigment manufacturer with stable and reliable quality and large production scale as the designated supplier. In addition, when purchasing pigments, quality factors such as durability should also be considered, otherwise color changes may occur during the stacking process, resulting in inconsistent surface color.
5.2.2 Regularly calibrate measuring equipment to reduce measurement errors.
6. Whitening on the surface in winter
6.1 Phenomenon and Cause Analysis
During the curing period of colored cement concrete pavement bricks, the excess mixing water in the concrete dissolves the calcium oxide formed by cement hydration, or the water outside the concrete dissolves the calcium oxide and seeps to the surface, reacting with carbon dioxide in the air to produce insoluble calcium carbonate, forming a whitening phenomenon. Due to the relatively rough surface of the colored cement concrete pavement bricks produced using this molding process, whitening is easily observed in winter.
6.2 Prevention and control measures
6.2.1 Improving the surface density of pavement bricks
6.2.2 Improve maintenance conditions.
6.2.3 Use admixtures.
6.2.4 Use high-quality pigments.
7. Conclusion
Reducing the occurrence of quality problems in colored cement concrete pavement bricks and timely prevention and control is of great significance for improving the production quality of colored cement concrete pavement bricks, reducing waste rates, and improving economic benefits.