Abstract: Currently, there are two main types of large tonnage hydraulic brick making machines in the market that use solid waste such as tailings, fly ash, coal gangue, construction waste, and steel slag as raw materials: one is the 1300 ton hydraulic brick pressing machine produced by Fujian Haiyuan Automation Machinery Equipment Co., Ltd; The other type is the 1280 ton hydraulic pressing brick machine produced by Henan Machinery Design and Research Institute Co., Ltd. At present, neither of these two types of brick machines can manufacture variable cross-section mortise and tenon type floor tiles, and there are also certain shortcomings in secondary replenishment. Therefore, a multifunctional hydraulic brick making machine has been designed that can manufacture mortise and tenon type variable cross-section bricks and achieve perfect secondary fabric.
Keywords: solid waste; Hydraulic brick making machine; Mortise and tenon type; Variable cross-section; Secondary fabric
0 introduction
At present, there are two main types of large tonnage hydraulic brick making machines in the market that use solid waste such as tailings, fly ash, coal gangue, construction waste, and steel slag as raw materials. One is the 1300 ton hydraulic brick pressing machine from Fujian Haiyuan Automation Machinery Equipment Co., Ltd., and the other is the 1280 ton hydraulic brick pressing machine from Henan Machinery Design and Research Institute Co., Ltd.
Due to its structural reasons, the Fujian Haiyuan brick making machine can only design the hopper and fabric truck for the base material and fabric for secondary fabric on one side of the brick machine, resulting in a secondary action after the brick clamping frame clamps the bricks. The bricks are easily damaged, the fabric is prone to waste, and the bottom surface of the bricks is prone to fabric floating ash. The machine is prone to damage, and the secondary fabric is only suitable for bricks with a flat bottom surface. If the bottom surface of the bricks that require secondary fabric is uneven, This type of brick machine cannot be used for secondary fabric distribution.
The disadvantage of the brick machine structure produced by Henan Machinery Design and Research Institute Co., Ltd. is that it cannot press porous bricks with variable cross-section core columns, and the secondary fabric design of this brick machine is generally the same as that of Haiyuan, Fujian.
The common feature of the two brick machines mentioned above is that they are currently unable to produce variable cross-section mortise and tenon type floor tiles (see Figure 1).
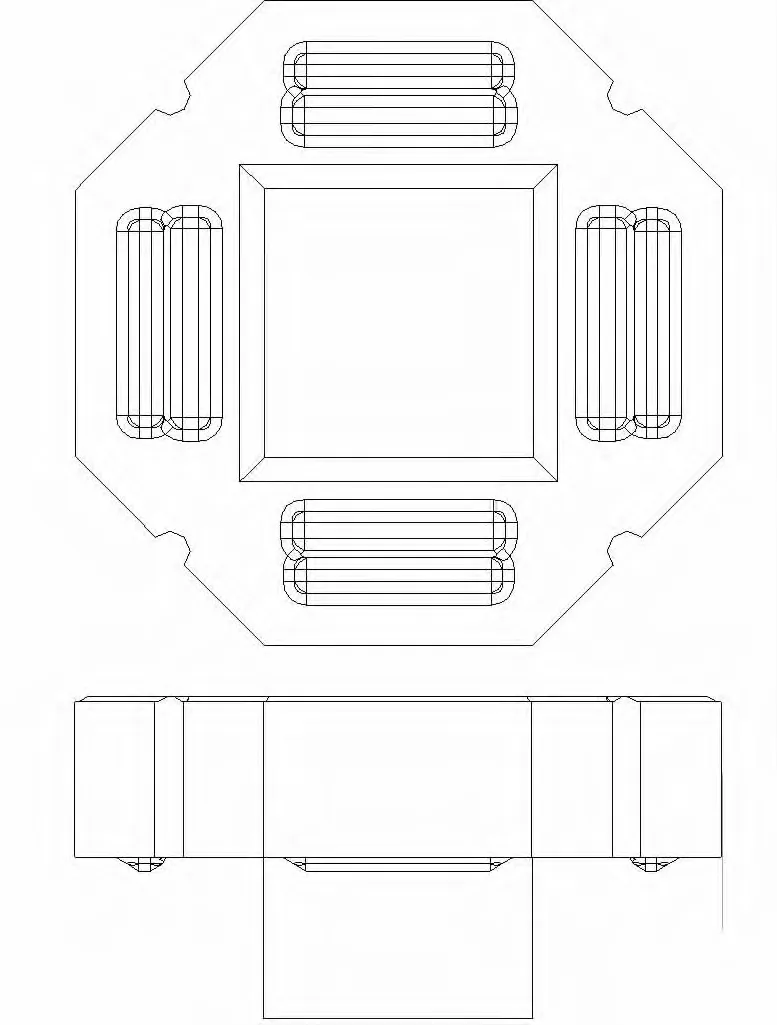
Figure 1 Variable cross-section mortise and tenon type floor tiles
To address the shortcomings of the above brick making machines, the author has designed a new type of hydraulic brick making machine. This brick making machine has the following advantages: in addition to manufacturing various standard bricks, hollow bricks, and road bricks, it can also manufacture mortise and tenon shaped variable cross-section floor tiles, which can perfectly solve the problem of secondary fabric distribution.
1. Main innovation points of hydraulic brick making machine
The structure of the hydraulic brick making machine designed in this article is shown in Figure 2. The main structure still adopts a four column structure, and the brick making machine mainly adopts two innovative designs: the first is to lay the fabric mechanism and brick clamping mechanism layer by layer on the connecting device (the connecting device is fixed and installed on the four columns), and the fabric distribution mechanism and base material distribution mechanism are distributed on both sides of the main body of the brick machine; The second innovation point is to connect and position the mold frame and lower mold with auxiliary oil cylinders and four columns, making it a whole assembly accessory. It is installed on the lower movable beam and can move up and down with the lower movable beam. The mold frame and lower mold can also move up and down with each other. By using these two designs, the problem of imperfect secondary replenishment can be solved, and a newly designed variable cross-section mortise and tenon mold (referring to patent CN109176838A, a floor tile mold and production method) can be equipped to manufacture variable cross-section floor tiles.
The main principle of innovation: Place the lower mold on the lower movable beam, arrange oil cylinders on the lower mold, and connect the oil cylinders to the mold frame. The main intention is to form a whole between the lower mold and the mold frame, which can remain stationary and move up and down with each other. The purpose of this design method is not only limited to demolding and floating the middle frame to make the brick dense, but also to improve the accuracy of brick production, The most important point is that the manufacturing of variable cross-section mortise and tenon type floor tiles can be achieved.
The existing technical solution has the following problems: when the fabric base material is arranged on one side, when the bottom surface of the brick is not a flat surface but uneven, the fabric needs to pass through the middle frame before the base material can be distributed. However, when the fabric distribution cart passes through the middle frame, the fabric will inevitably be distributed on the concave part of the brick, as shown in Figure 1, with a concave and convex surface at the middle variable cross-section plane; Like other brick types, which have tapered holes inside, when the fabric passes through, it will inevitably cause a large number of gaps between the conical column of the mold and the straight hole of the lower mold to leak out.
In order to solve the above problems, this design distributes the base material and fabric fabric distribution mechanism on both sides of the brick machine body, and arranges the brick clamping mechanism below the fabric distribution mechanism. It should be emphasized here that the way the brick body is pulled out of the mold from below the mold frame is not applicable to the above-mentioned irregular brick shapes. When fabric is needed, the lower mold and mold frame of this design need to maintain a relative position, while rising to the upper plane of the mold frame and fitting with the lower plane of the fabric mechanism, to achieve separate fabric distribution between the base material and the fabric, and ultimately press and form. When the bricks are removed from the mold frame, it is necessary to ensure that the lower mold and the mold frame remain in relative position, while also ensuring that the upper plane of the mold frame is in contact with the lower plane of the brick clamping mechanism, in order to ensure that the cloth is placed on one plane and the bricks are clamped on another plane, and the cloth and brick clamping mechanisms do not interfere with each other. Based on this operating principle, the starting point of the hydraulic brick making machine designed in this article is to ensure that the lower mold and mold frame are connected as a whole through the lower movable beam and the auxiliary oil cylinder of the lower mold, while also being able to move up and down with each other.
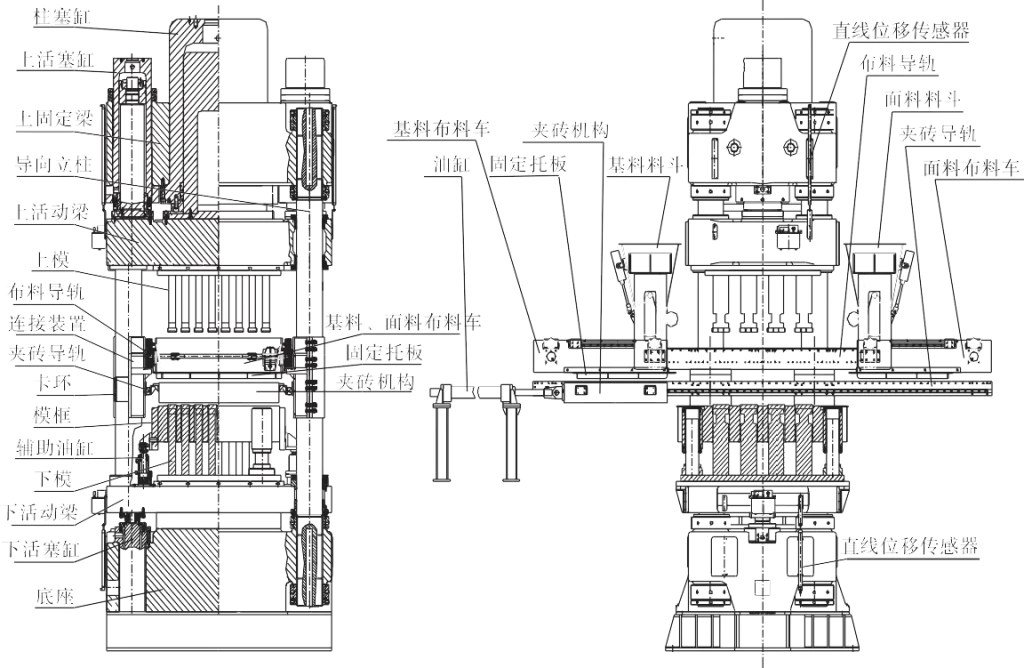
Figure 2 Hydraulic Brick Making Machine
2. Finite element analysis of main structural components
Verify the stress and deformation of the plunger cylinder barrel, upper fixed beam, upper movable beam, and base under working pressure using finite element analysis to determine whether the design meets the actual usage requirements. The cylinder barrel is analyzed using SolidWorks Simulation, the fixed beam and base mesh are divided using Hypermesh, and the stress-strain analysis is conducted using ABAQUS.
2.1 Selection of physical performance parameters for cylinder material
According to the “Mechanical Engineering Material Performance Data Manual”, the material’s elastic modulus at room temperature is 209 × 105 MPa, shear modulus 82.3 × 103 MPa, Poisson’s ratio 0.269, yield strength 355 MPa, input the parameters into the analysis software.
2.2 Establishment and Simplification of Cylinder Barrel Model
Considering the symmetrical structure of the cylinder barrel, a 1/2 model is taken for analysis to reduce the computational complexity by half and facilitate the visualization of stress distribution on the interface; And the layout of the system determines that the bolts only have a fixed effect, simplifying the bolt structure to speed up the calculation speed, and preliminary analysis shows that there must be stress concentration at the oil inlet.
2.3 Cylinder Grid Division
Perform grid division on the cylinder barrel, and due to the problem of stress concentration at the oil inlet, refine the grid here to obtain accurate analysis. The maximum aspect ratio of grid quality is 18.6, less than 30, and the maximum Jacobian ratio is 14.3, less than 30, with the maximum value far from the oil inlet. The total number of grid nodes is 80495, the total number of units is 52704, and the Jacobian points are 4. The unit size is 80mm, and the grid quality is high. The above can meet the analysis accuracy requirements.
2.4 Setting of cylinder boundary conditions
Symmetrical plane symmetry constraint (limiting 1 degree of freedom for movement and 2 degrees of freedom for rotation) with 2 degrees of freedom for displacement on the bearing surface, simulating the displacement constraint of the fixed beam and bolt on the cylinder (the bolt constrains the radial displacement, but this force is very small, so the influence of bolt loading on the entire bearing surface result is omitted).
2.5 Loading load
The rated load of the oil cylinder is 25 MPa, and the right end cover of the cylinder acts as a sealing device. When the cylinder is working, the equipment is connected here, and the end cover is not load-bearing. The strength grade of the material at the weld seam of the cylinder barrel is higher than that of the base material. In this analysis, the same structural material was used instead, and the results are biased towards safety. The analysis is based on the premise that the material is uniform, all properties are the same, and the weld seam is free of defects, excluding the weakening of strength caused by manufacturing defects.
2.6 Cylinder Load Loading
Load the rated load (25 MPa) at the maximum working condition (worst working condition) of the cylinder pressure surface after the plunger is extended.
2.7 Calculation results of cylinder barrel rated load conditions
The node stress cloud diagram of the cylinder barrel is shown in Figure 3, and the 400 fold combined displacement cloud diagram is shown in Figure 4. By doubling the grid of the cylinder barrel and recalculating, it was found that the maximum stress in the cylinder barrel increased from 200.31 to 199.49 (with slight changes in position and minimal impact), and the numerical change was only (200.31-199.49)/200.31=0.41%<5%. Therefore, it can be determined that the calculation accuracy is sufficient.
Looking at the stress again, the maximum stress is only 200.31 MPa, less than 355 MPa, fully meeting the material strength requirements, with a safety factor of 355/200.31=1.77.
Finally, looking at the radial displacement and combined displacement, the extreme values are only 0.18 mm and 0.21 mm, and the structural stiffness can meet the usage requirements.
2.8 Calculation results of test load conditions
Considering the test load conditions, modify the load from 25 MPa to 37.5 MPa to verify whether the structure can meet the strength requirements under the test load conditions through analysis. After calculation, the maximum stress of the cylinder barrel is 299.23 MPa, which is less than 355 MPa. It can be seen that the structure can also meet the strength requirements under test load conditions.
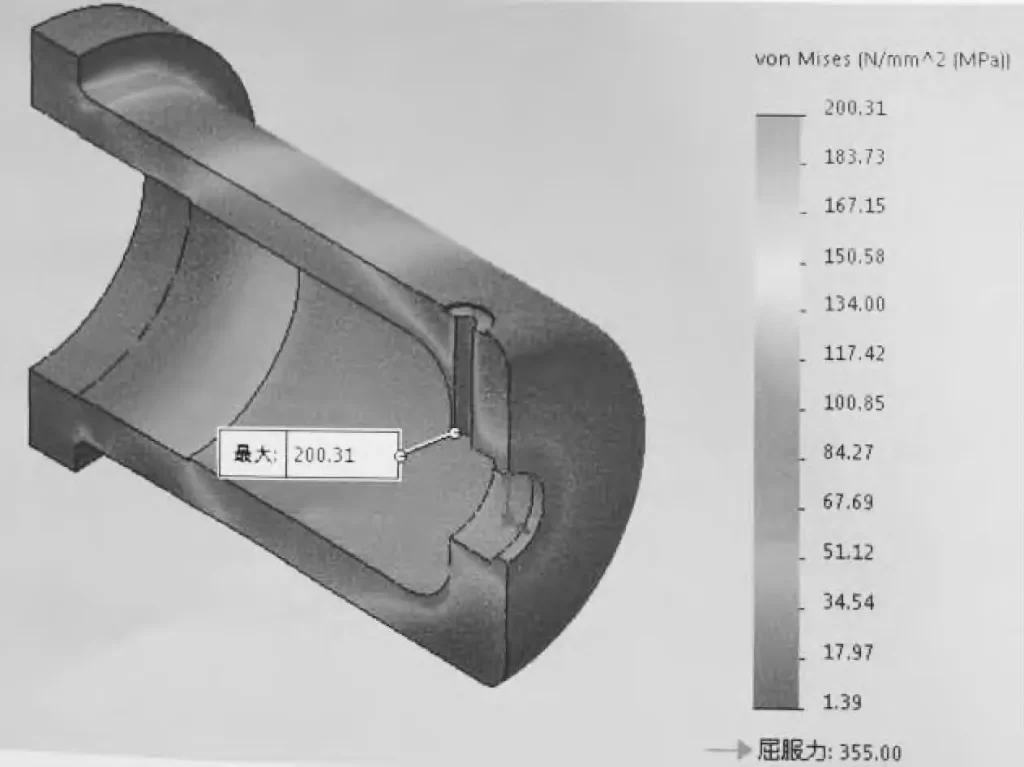
Figure 3 Cloud Chart of Cylinder Tube Node Stress
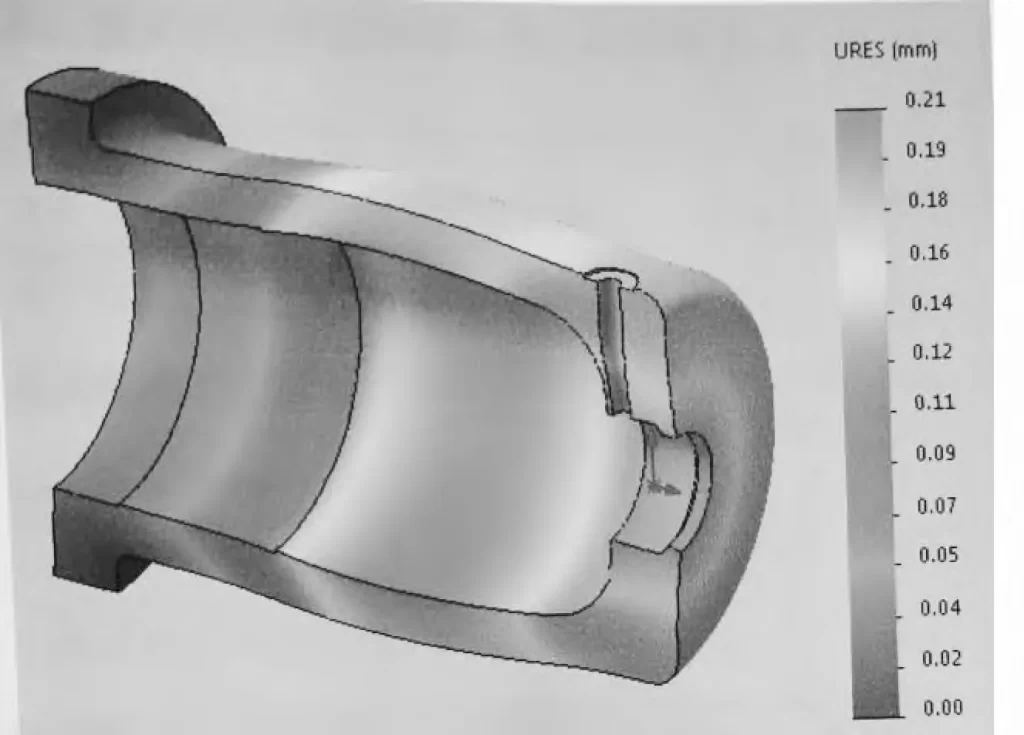
Figure 4 Cloud Chart of Cylinder Barrel 400 Times Closing Displacement
2.9 Brief calculation instructions for upper fixed beam and base
The stress cloud diagram of the upper fixed beam is shown in Figure 5, with a maximum stress of 145.2 MPa, less than 370 MPa. The stress cloud diagram of the base is shown in Figure 6, with a maximum stress of 152.5MPa, which is less than 370 MPa. Meet design requirements.
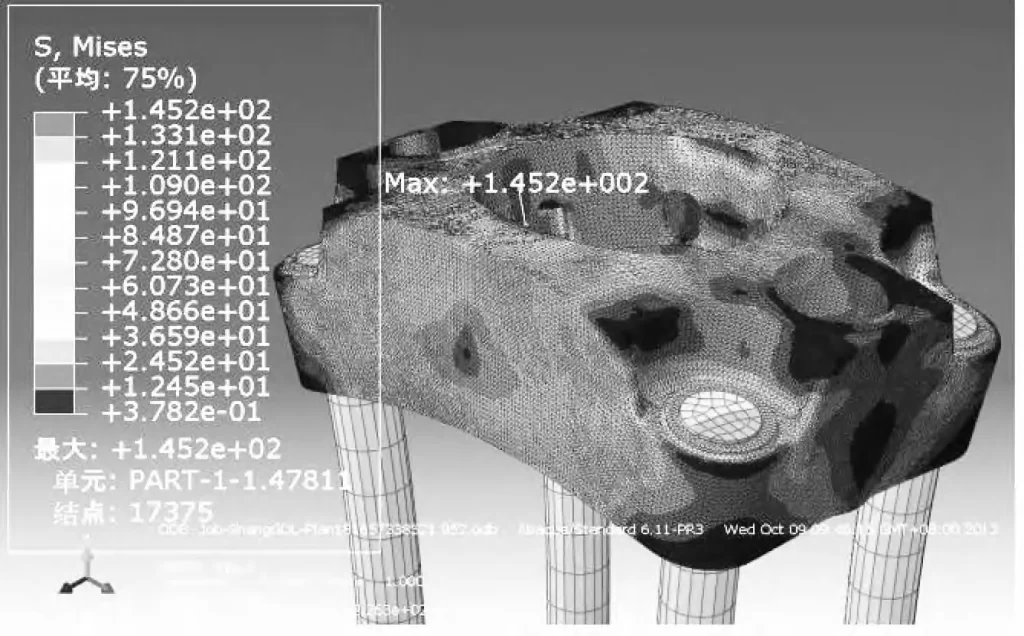
Figure 5 Stress Cloud Map of Upper Fixed Beam
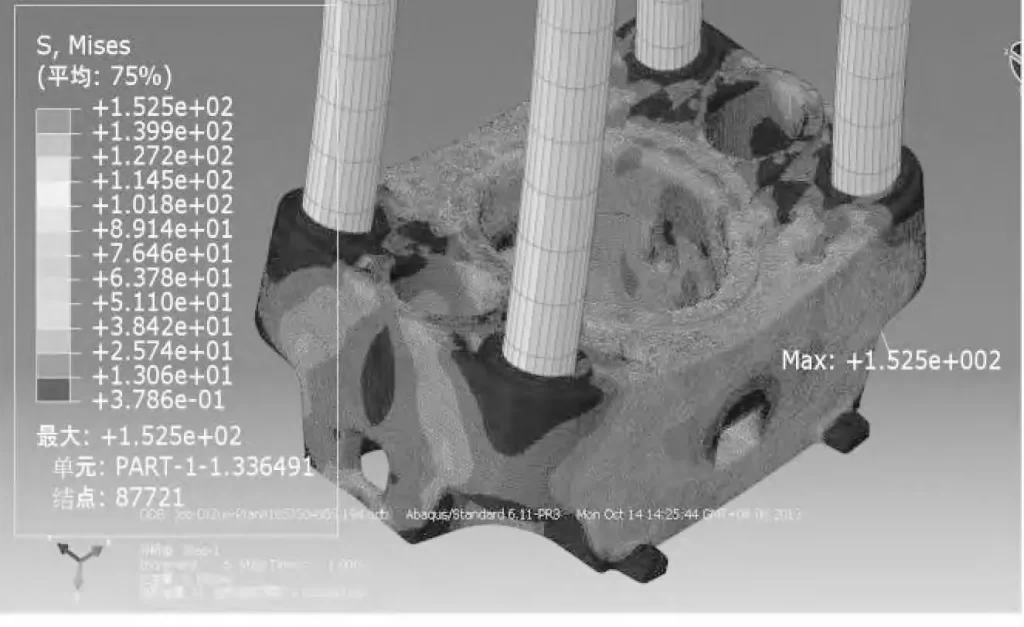
Figure 6 Base Stress Cloud Chart
3. Application effects
The hydraulic brick making machine designed in this article has been successfully trial produced and has achieved semi automation without a large production line and equipped with a small amount of auxiliary equipment. It can achieve the manufacturing of variable cross-section mortise and tenon type floor tiles in large quantities. Other brick types such as urban road bricks, square bricks, mortise and tenon type wall bricks have been manufactured on this brick machine, and the application effect is very good, which is gradually being promoted and applied.
4. Conclusion
The hydraulic brick making machine designed in this article provides for the first time a brick making method that uses solid waste such as tailings, fly ash, coal gangue, construction waste, steel slag, etc. as raw materials to manufacture various standard bricks, hollow bricks, road bricks, mortise and tenon type wall bricks, mortise and tenon type variable cross-section floor tiles. This brick making method can be used to manufacture mortise and tenon type variable cross-section floor tiles and provide secondary fabric. The hydraulic brick making machine adopts a flexible design and can choose different configurations according to customer needs, achieving customer needs for brick shapes at the minimum cost, while solving the problems existing in existing technical solutions.