Abstract: This paper presents the logic comtrol of a brick machine based on the Siemens S7-200 type PLC.The software and hardware of the system are discussed.
Keyword: PLC; brick machine ; hardware software design
1. introduction
In recent years, with the improvement of automation technology in China, factory automation has also reached a new level. As an emerging industrial controller, PLC has unique advantages in small size, complete functionality, low price, and high reliability, and has been widely used in various fields. The brick industry is an essential component of the construction industry, and its development directly restricts the development of the construction industry. However, the current control system of brick making machines is still manually operated, far from keeping up with the pace of the times, and urgently needs reform. This article introduces the principle, structure, and control system of an automatic brick making control system based on actual production needs. It can achieve automatic production throughout the entire process of feeding, feeding, forming, demolding, and brick discharging.
2. technological requirements
2.1 Control System Requirements
(1) By controlling the advance and retreat of the mold cylinder, hydraulic cylinder, feeding cylinder, etc. through PLC, the performance of the system is improved and manpower is reduced; By changing the mold, different specifications of porous brick hollow blocks, curbstones, road bricks, as well as cement products such as grass tree bricks and slope protection bricks can be produced; Each action program is interlocked.
(2) Manual/automatic buttons have been set. If the manual button is used during system or software debugging, in general production, automatic mode is used. And indicator lights have been set for each button to facilitate error detection when the system is not functioning properly.
(3) Each signal has an indicator light to prevent management and inspection errors.
2.2 Process Flow Diagram
From the process flowchart, it can be seen that the brick making process involves sending the push plate to the workbench at the bottom of the mold box, raising the workbench to the bottom of the mold box, lifting the mold, and pouring the mixed and stirred materials into the mold through a reciprocating guide fabric device. The mold box vibrates, and the upper pressure head presses down to compact and shape the materials in the mold box while vibrating; Determine whether a secondary fabric is needed. If necessary, return to feeding. If not, the workbench will drive the push plate and formed brick down to the bottom, and then push the push plate and formed brick out together to complete the brick making work.
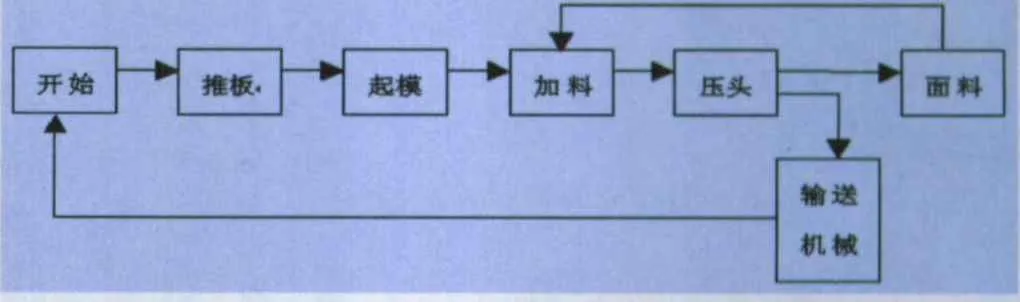
Figure 1 Industrial Process Diagram
2.3 I/O points and address allocation of the control system
The input/output signal names and address numbers of the control system are listed in Table 1.
According to the process requirements and actual production needs, the following sequential functional diagrams have been designed (see Figures 2 and 3), where Figure 2 is the functional diagram during shutdown and Figure 3 is the production process control diagram. The engineering diagram of the shutdown is shown in Figure 2-1. After pressing the shutdown button, the fabric cylinder will retract, the mold cylinder will retract, the pressure head cylinder will retract, and the push plate will retract. Then, stop the brick mold motor and oil pump motor, and the entire system will safely stop.
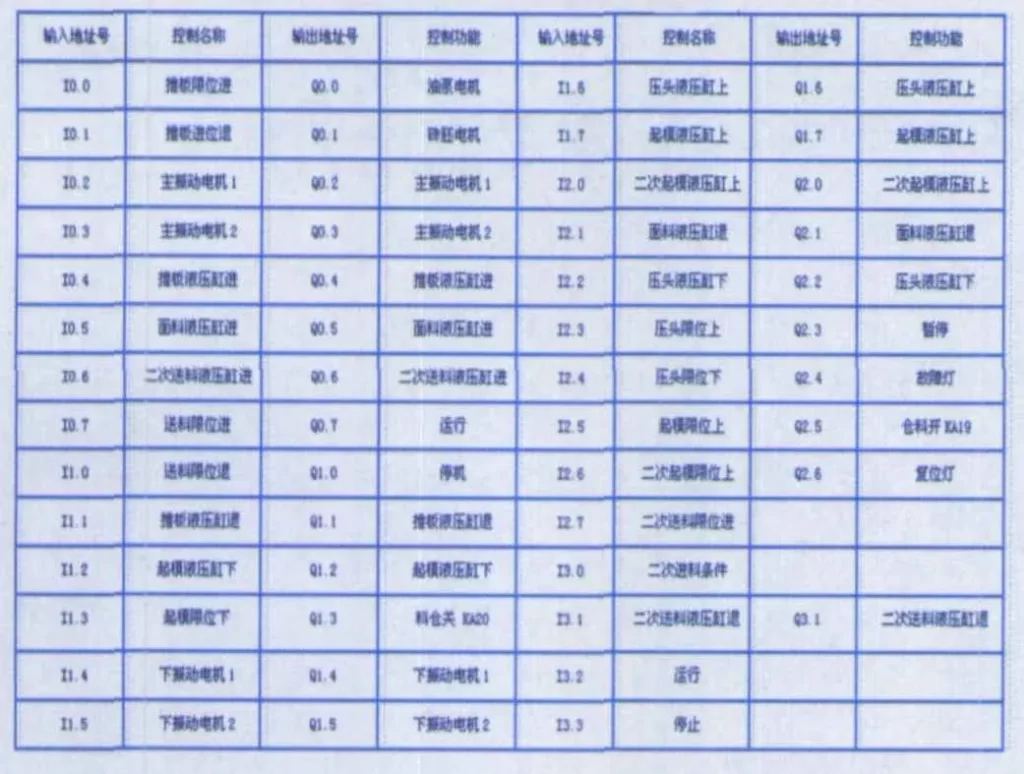
Table 1 Codes and Address Numbers
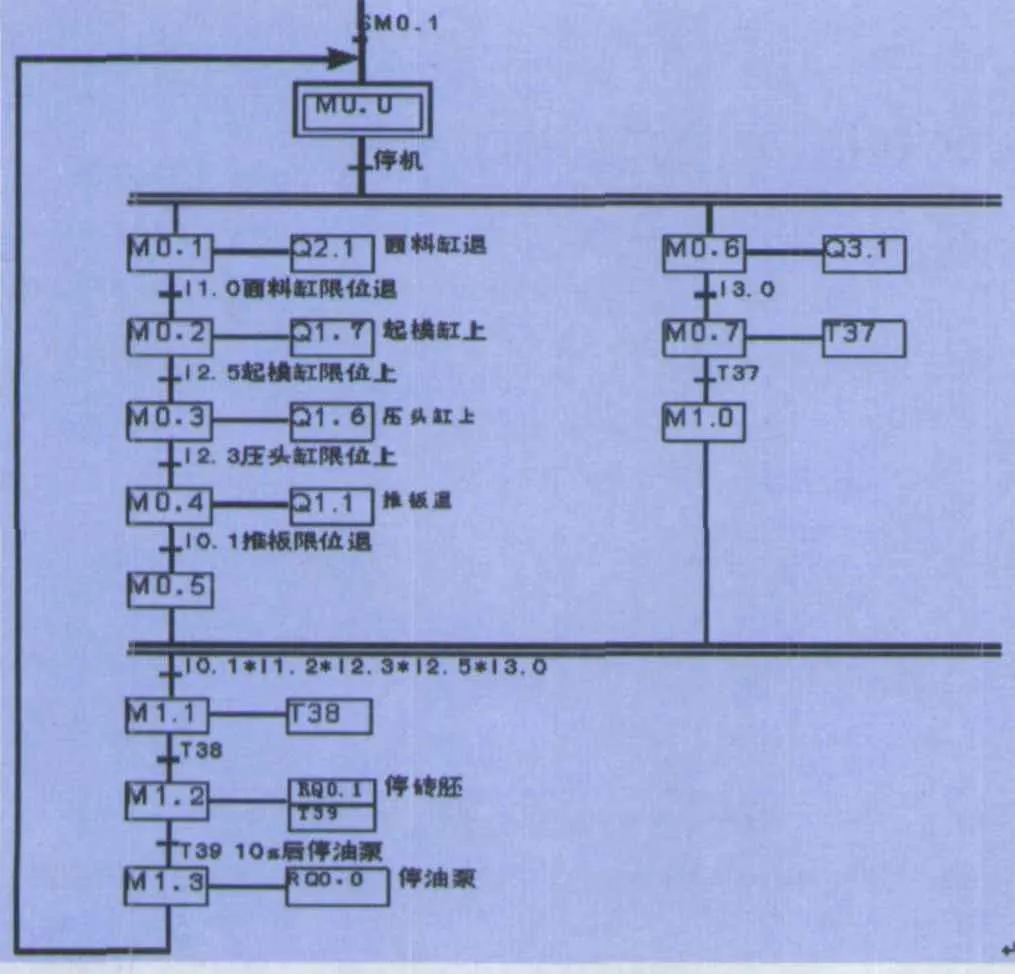
Figure 2 Functional diagram of shutdown sequence
The control diagram of the production process is shown in Figure 3. When the output addresses Q0.0 and Q0.1 are in 1 state, Q1.0 is in 0 state, and Q0.7 changes from 0 to 1, the control system begins to operate. When Q0.4 is ON and M0.1 is set to control the push plate movement, and the travel switch I0.0 is ON, the program is divided into two parallel branches. Branch 1: M0.2 is set, Q1.2 is activated to control the lower part of the mold cylinder. When the travel switch I1.3 is ON, the mold cylinder stops, M0.3 is set, Q0.5 is activated, and the feeding cylinder enters in sequence. This branch completes the following tasks in sequence: the feeding cylinder feeds the raw materials into the mold cylinder, and at the same time, the lower vibration motors Q0.2 and Q.3 are activated to help feed the materials into the mold cylinder. The time relay controls the switch of the material bin to ensure sufficient raw materials, Then start the main vibration motor and the pressure head motor to compact the raw materials, and then reset the main vibration motor. On the mold cylinder, the pressure head motor stops. Branch 2: After the time set by T44, the push plate retracts, and then resets Q1.1 and Q0.4, which control the motor for the push plate hydraulic cylinder to move forward and backward. Then, it determines whether a secondary fabric is needed, that is, whether Q0.7 is 0 or 1. If it is 0, the program ends, and the cycle runs again from the beginning. If it is 1, it continues to add secondary fabric. M2.6 is set, Q0.6 acts, and controls the secondary fabric to move forward. When I2.7 is ON, the secondary fabric retracts, and then resets, while also starting the mold cylinder, On the pressure head cylinder, the process ends and returns to the initial state, executing in a cycle.
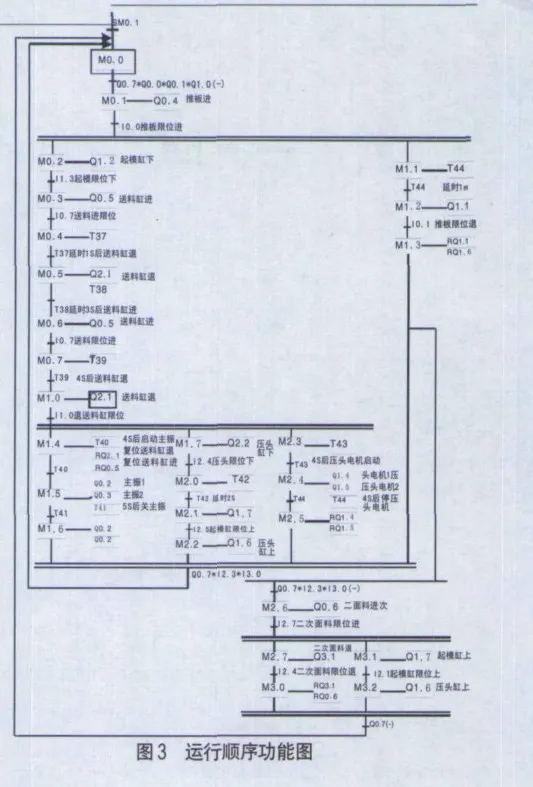
Figure 3 Functional diagram of operation sequence
3. hardware design
Programmable Logic Controller (PLC) is a universal automatic control device. It integrates computer technology, automation technology, and communication technology, becoming the core equipment for modern industrial automation. Applying PLC and computer control technology to the control system of brick making machines and implementing interlocking protection, automatic control, and process control through software design can undoubtedly solve the problems existing in the current brick making system. The lower computer uses Siemens’ S7-200 series PLC as the control system core. This type of PLC combines the advantages of modular and integrated PLCs, that is, the CPU itself comes with a certain number of digital I/Os that can independently complete switch control. At the same time, it has scalability and can be combined with digital I/O modules, analog I/O modules, and communication modules to form complex systems. This series of PLCs has the advantages of compact structure, low price, excellent performance, large program capacity, fast running speed, flexible programming, and powerful communication functions, making them particularly suitable for small and medium-sized control systems.

Figure 4 System Configuration Diagram
3.1 PLC system selection
From the above analysis, it can be seen that the system has a total of 27 switching input points and 23 switching output points; If CPU 226 PLC is selected, expansion units are still required, and the price is high, resulting in significant waste. Referring to the Siemens S7-200 product catalog and actual market prices, selecting a CPU 224 (14 input/10 output) as the host, and adding a hybrid expansion module EM223 (16 point input/16 point output) is the most economical configuration. The configuration of the entire PLC system is shown in Figure 4.
3.2 System Control Schematic Diagram
Figure 5 shows the control schematic diagram of the PLC system, which can be used continuously after being connected. Even if the process changes, only the software design needs to be changed without changing the wiring.
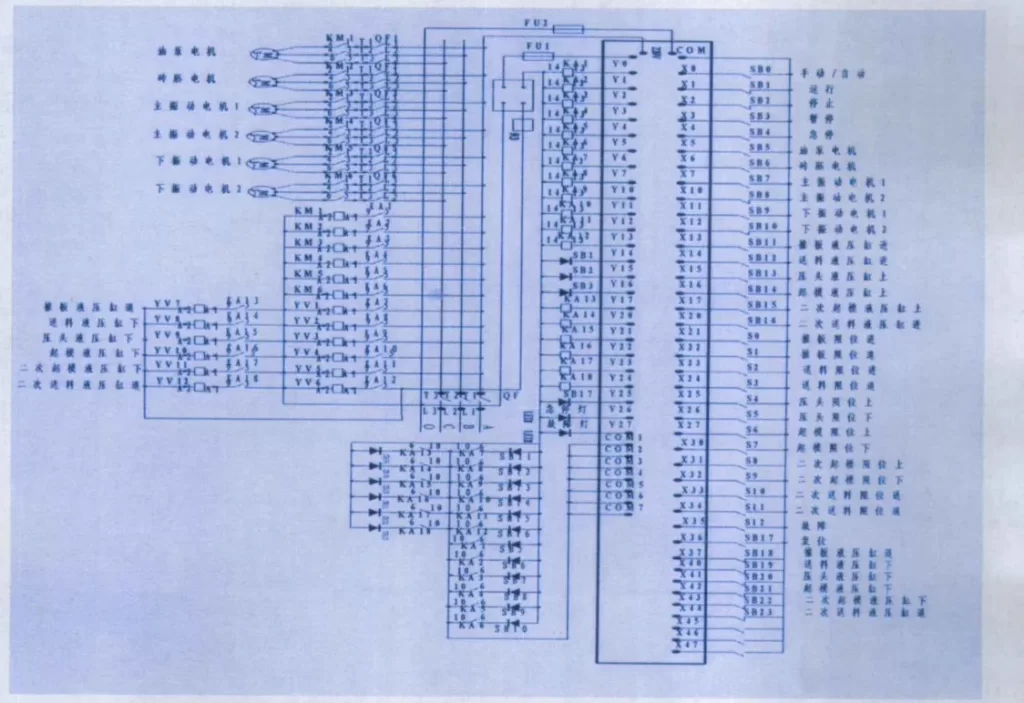
Figure 5 System Control Schematic Diagram
4.software design
Based on the analysis of the composition and control principle of the brick making machine system, the software of the brick making machine control system consists of the following program modules, as shown in Figure 6.
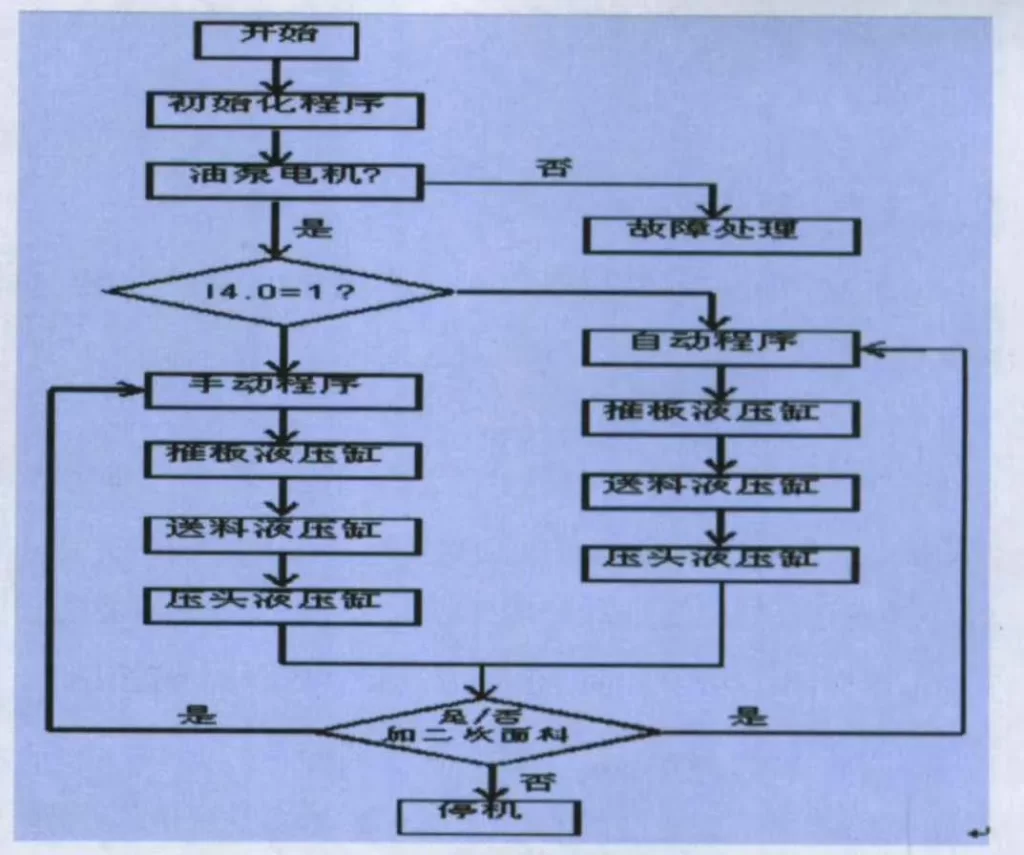
Figure 6 Software flowchart
Initialization program: Set system initialization parameters, clear and reset some data registers and timers.
Single step debugging program: used for system debugging, for maintenance personnel to use. After entering this program, the interlocking conditions are lifted, and the equipment is completely controlled by manual control to start the fault handling program for each component; Handling system faults displays different fault categories based on the different types of input signals, attracting the attention of operators and assisting maintenance personnel in repairing equipment, ensuring equipment safety and personal safety.
Emergency stop program: When the system malfunctions, this emergency stop program can immediately stop the system.
Automatic program: The system adopts automatic mode to automatically enter the control of the brick making system.
Manual program: used for manual brick making.
Public program: System function call for common use by program modules.
Communication program: used when the system communicates with other systems.
Shutdown program: When executing this program, the PLC shuts down all components, power supplies, motors, and valves in sequence according to the operating status of the equipment.