Abstract: Green environmentally friendly cement bricks can realize the reuse of resources and protect China’s land resources, which are being used more and more widely. This paper introduces a mechanical equipment that uses industrial waste, construction waste, river sand, coal gangue and cement to scientifically match, vibrate and press into various shaped environmentally friendly cement bricks. The machine has the advantages of simple structure, easy maintenance and low production cost, and the social and environmental benefits are outstanding.
Keywords: green environmental protection; vibration suppression; cement brick; mechanical equipment
0. Introduction
In recent years, with the continuous deepening of urbanization, environmental protection and green municipal engineering have been increasing. Traditional clay bricks, due to their destruction of resources and environmental pollution, can no longer meet the requirements of the times [1-2]. Green and environmentally friendly cement bricks, due to their protection of China’s precious land resources and the realization of resource reuse, are increasingly being widely used. Environmentally friendly bricks are a new type of wall material manufactured without high-temperature calcination, using coal slag, coal gangue, fly ash, tailings, chemical slag, natural sand, marine mud, industrial waste, waste incineration slag, etc. as the main raw materials. It is also in line with China’s general policy of “protecting farmland, conserving energy, adapting to local conditions, and using local materials” for the development of building materials. Environmentally friendly bricks are building materials products that are fully exempt from value-added tax. Due to its high strength, good durability, standardized size, complete appearance, and uniform color, this material has a simple and natural appearance, and can be used as a clean wall or any external decoration. Therefore, it is a highly promising replacement product for clay bricks. Compared with clay bricks, cement bricks utilize industrial waste residue and do not require sintering and steam curing, resulting in low production costs, large slag consumption, and outstanding social and environmental benefits.
This machine is a mechanical equipment that utilizes raw materials such as industrial waste, construction waste, river sand, coal gangue, etc., and adds a certain amount of cement. After scientific mixing, it is evenly mixed through a small mixer or manual mixing, manually operated, and vibrated to form various irregular cement bricks. Suitable for making shapes smaller than 200 mm × 500 mm paving bricks with a thickness of 60-100 mm can be produced using molds of different shapes, including I-shaped, rectangular, square, and bone shaped paving bricks. The mold replacement is convenient and simple, and maintenance is convenient. The cement bricks produced do not need to be sintered, but are made by drying them for a short period of time and natural curing. The brick production effect is good, it is easy to reach the specified strength, and it saves cement and other raw materials compared to static pressure equipment. Widely used for laying sidewalks on both sides of roads and garden roads. Utilizing this brick making machine to produce green and environmentally friendly cement bricks has the advantages of low investment and quick results, making it a popular industry for investment at present.
1. Structural form of brick making machine
This machine mainly consists of 9 parts, as shown in Figure 1. The mold lifting mechanism is located on the frame, and the mold includes an upper mold and a lower mold, which are located directly above the mold lifting mechanism. The upper mold control assembly is fixedly connected above the mold, and one end of the rotating assembly is fixedly connected to the frame, while the other end is fixedly connected to the upper mold control assembly. The vibration components are located below the mold lifting mechanism and connected to the mold lifting mechanism. The diesel engine assembly is located on one side of the frame, and the diesel engine assembly is connected to the vibration components through a triangular belt.
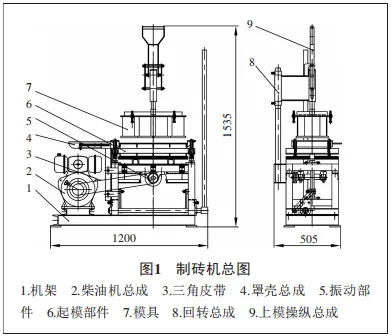
Figure 1
The above molds are of different shapes and can produce various irregular paving bricks such as I-shaped, rectangular, square, and bone shaped. The vibration components include bearing seats, eccentric shafts, pulleys, gaskets, and bolts. There are two bearing seats, each fixed to the frame. One end of the eccentric shaft is located on one of the bearing seats, and the other end extends outward through the other bearing seat. The pulley is located on the periphery of the extension part of the eccentric shaft, and the outer side of the pulley is fixed to the pulley through gaskets and bolts, which can generate excitation force to achieve vibration and achieve dense bonding of materials. Belt pulley with built-in clutch device; It can achieve belt pulley clutch, thereby controlling excitation time and intensity, and improving efficiency. The outer circumference of the bolt end is equipped with a spring washer; Due to vibration during operation, it can prevent bolts from loosening due to prolonged vibration. There is a cover above the diesel engine assembly, which includes a cover body, an excitation operating mechanism, a bracket, and a connecting plate; There are two brackets arranged in parallel, each with an upper and lower connecting plate. The bracket is connected to the frame through the connecting plate, and one end of the cover body is vertically connected to the two brackets, while the other end extends above the diesel engine assembly; The excitation operating mechanism includes an excitation mechanism and a throttle cable; The excitation mechanism is hinged with the hood, and one end of the throttle cable is connected to the excitation mechanism, while the other end is connected to the diesel engine throttle. Due to the fact that the exhaust device of the diesel engine is located on the upper part of the diesel engine, the muffler of the exhaust pipe heats up when the diesel engine is working, and the operator may be scalded if accidentally touched. The cover can provide safety protection and firmly connect the excitation operating mechanism. By manipulating the handle of the excitation mechanism to rotate and control the length of the throttle cable extension, the size of the diesel engine throttle is controlled to achieve speed changes, and the clutch inside the diesel engine belt plate is activated. The vibration is transmitted to the bottom of the lower mold through the belt to achieve excitation and control the intensity and time of excitation.
2. Working principle and operating steps
Working principle: The vibration component uses a diesel engine as the power source and is transmitted through a triangular belt to the vibration generating component for excitation. Under the excitation force, the material particles generate strong motion in the direction of vibration, and the gaps are filled in the movement of the material to achieve a dense combination, resulting in high strength. There is no need for complex gear connecting rod systems and specialized vibration boxes with high manufacturing costs [8-9]; The mold lifting mechanism drives the lower mold to move up in a straight line. During this process, the upper mold keeps pressing on the brick blank, and the lower mold continues to move up. After the brick blank is released from the mold cavity, the lower mold drives the upper mold to move up together, achieving complete demolding.
As shown in Figure 1, the specific operation steps of the brick making machine are as follows: 1) Lift the handle 9 of the upper mold control assembly to completely detach the upper mold of mold 7 from the lower mold, and rotate the upper mold around the rotation axis 8 to the 90 ° side; 2) Pull and press down the handle 6 of the mold lifting mechanism slightly to expose the gap between the lower mold and the base, then place the special support plate and reset the handle 6 of the mold lifting mechanism; 3) Inject any one or more types of materials such as industrial waste, construction waste, river sand, and coal gangue into the lower mold, mix them evenly with cement, mortar, and water, and spread them evenly. Rotate the upper mold to return to its position and press down on the handle 9 of the upper mold control assembly to make the upper and lower molds fit together, pressing down on the materials in the lower mold cavity; 4) Start the diesel engine and adjust the clutch device through speed. The triangular belt 3 drives the vibrating component 5 to vibrate, causing the material in the mold cavity to vibrate tightly; 5) Pull the operating handle of the lifting mechanism 6 to drive the lower mold to move up in a straight line. During this process, the upper mold keeps pressing the brick blank, and the lower mold continues to move up. After the brick blank is released from the mold cavity, the lower mold drives the upper mold to move up together, achieving complete demolding; 6) Remove the bricks together with the pallet, place them in a cool and dry place for maintenance, and then place them in the next pallet for the next cycle.
3. Main structural features
This machine has two main characteristics that differ from other cement brick making machines in terms of structure: firstly, it uses a mechanical linkage mechanism to achieve compression and demolding actions; The second is to use an eccentric shaft to achieve vibration forming. Utilizing an eccentric shaft to achieve vibration excitation makes the machine structurally simple and practical.
The working principle is as follows: the vibration part uses a diesel engine as the power source, and is transmitted through a belt 3 to the eccentric shaft component 2 that generates excitation to achieve vibration. Under the excitation force, the material particles generate strong motion in the direction of vibration, and the gaps are filled in the movement of the material, achieving a dense combination and generating high strength. The diesel engine pulley 4 is equipped with a built-in clutch device, which uses the control of the diesel engine throttle to make the engine run fast or slow to achieve pulley clutch, thereby controlling the excitation time and strength. It has high efficiency and does not require complex gear connecting rod systems and a specialized vibration box with high manufacturing costs [10-12]. The structure is simple and practical, making it an ideal small-scale brick making machine vibration device. The vibrating pressure type brick making machine has better brick production effect than the static pressure type brick making machine, easy to achieve strength, and saves cement and other raw materials compared to the static pressure type equipment [13-14].
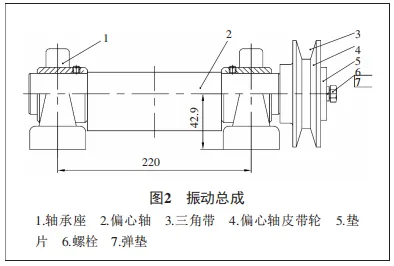
Figure 2
The fast and slow operation of the diesel engine achieves the clutch of the pulley, which is controlled by the throttle cable 3 and excitation mechanism 2 installed on the housing bracket 1.
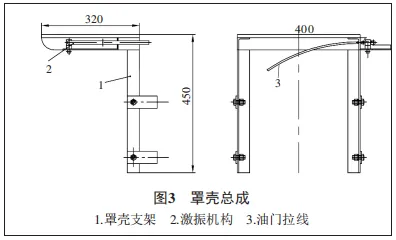
Figure 3
4. Conclusion
At present, some regions in China are still using sintered bricks, which has led to the destruction of more and more arable land, resulting in a significant loss and waste of land resources. At the same time, when sintering in a brick kiln, a large amount of harmful gases are generated, seriously polluting the environment. The country has issued a clear ban on the use of sintered clay bricks, advocated the construction of green and environmentally friendly homes, and strongly supported the use of new building materials. Cement bricks have a relatively light weight and high strength, and do not need to be fired. They are made of pollutant fly ash, which is relatively environmentally friendly. The country has been vigorously promoting them [15].
This machine has a simple structure, easy maintenance, low investment, and fast effectiveness. The cost price of each machine is around 7000 yuan. The operation is simple and flexible, and can be operated by one person. The operator does not need much theoretical knowledge, as long as they know the proportion of sand, stone, and cement for paving bricks, and the labor intensity is not high. By replacing different molds, various types of paving bricks can be produced, and mold replacement is convenient. Construction can be carried out in remote areas and without electricity, which is a way to achieve wealth and employment in remote areas. Suitable for use in households and small construction sites, it is convenient, flexible, and widely used, with considerable market prospects and broad development market [16].