Abstract: China’s annual production of fly ash ranks first in the world and will continue to grow in the future. The effective utilization of fly ash is also one of the urgent problems to be solved. The application of the three beam and four column hydraulic fly ash brick making machine has developed under this research background. The ingredient system is also one of the ways to ensure the performance of fly ash bricks. The batching system consists of three cans and one bracket, each used to hold fly ash, cement, and water. It is controlled by a PLC control system to automatically add, mix, and transport materials, achieving fully automatic control and improving efficiency.
Keywords: Fully automatic hydraulic brick making machine; Batching system; Structural design
1. Background and significance of the research topic
As of the end of 2017, China’s fly ash production reached 686 million tons, a year-on-year increase 4.7%, ranking first in the world in production, and will continue to maintain a growth trend in the future.A group of specialized fly ash comprehensive utilization enterprises have emerged, and fully automatic hydraulic brick making machines have developed under this background. One type of down pressure (bottom-up) frame hydraulic brick making machine has been widely used.The working device of the brick making machine is a three beam and four column frame structure, controlled by a hydraulic system. The batching system is controlled by a PLC system, which can achieve automatic material proportioning, mixing, transportation, and other production processes, achieving an annual output of 360 million bricks, fly ash bricks. Reference provides a detailed design of the working device, but lacks design analysis of the batching system.The structure of the batching system is directly related to the accuracy and effectiveness of material weighing, and is one of the important conditions for achieving full automation.
2. Structural Design of the Batching System for a Fully Automatic Hydraulic Brick Making Machine
2.1 Structural Scheme Design
The purpose of the structural design of the batching system is to ensure stable and orderly transfer of materials during the feeding process, and to distribute the materials in a simple manner to avoid a decrease in batching accuracy caused by the mixing of different materials. This facilitates the accurate weighing of different materials in the subsequent sequence. The structural design is composed of three material tanks and one bracket (three legs) (as shown in Figure 1).
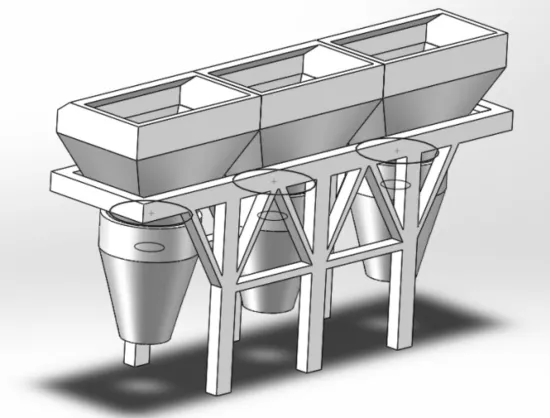
Figure 1 Assembly
The batching system is a fully automated production process with real-time mixing control. Solid powder and liquid materials can be mixed according to different ratios: different raw materials are transported and fed to three different material tanks A, B, and C through feeding fans. A dust removal device is installed above each tank to prevent foreign objects from falling into the tank and causing inaccurate batching. In the actual feeding process, material clumping may occur, The design is equipped with an excitation device. Once the material blocks the pipeline, activating the excitation button will prevent this phenomenon from occurring.The material transportation for each material pipe adopts a spiral feeding method, while setting the ingredient ratio, which can set the measurement and frequency of different materials. When the three materials are transported to the mixing tank in sufficient proportion, a weight signal will be transmitted to the PLC, and after the mixing is completed, they will be transported by a small car in a circular manner.
2.2 Finite element strength analysis
Using solidworks software for 3D design and modeling, generate/. X_ Save the t file to obtain the three-dimensional model of the ingredient system structure, and then import it into ANSYS software using automatic grid division mode. Find the “Supports” in the main interface
Click on ‘Fixed Support’, select the grounding area of the support leg as the support surface (fully constrained), and finally click on ‘Apply’ to apply. Find the ‘Force’ in ‘Loads’ and click on it. Select the upper end face of the support bracket downwards as the direction of pressure application, select’ components’ in the ‘define by’ option, apply a force of 160000N in the Z-axis direction, and click ‘Solve’ to complete the application of the original solid boundary conditions and load, Perform the solution (as shown in Figure 2).
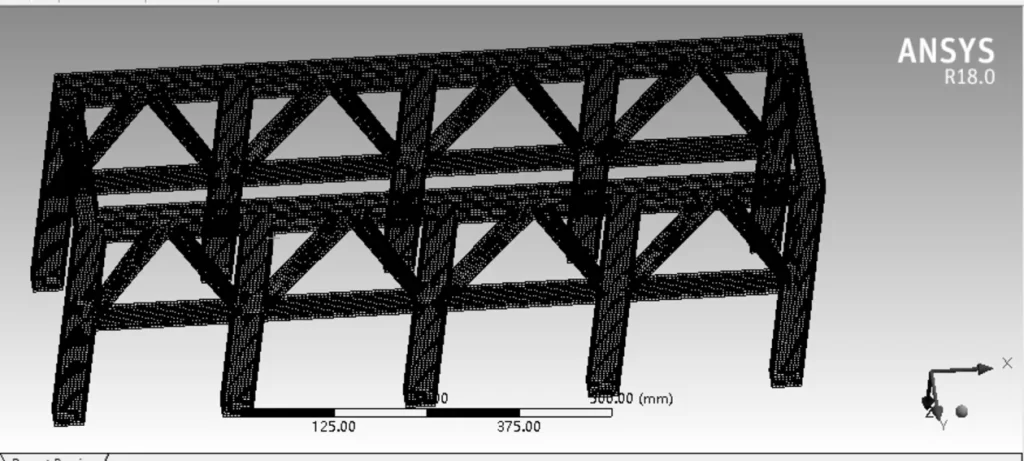
Figure 2 Gridding of Support Units
The equivalent stress cloud map and equivalent deformation cloud map of the bracket were obtained through post-processing, as shown in Figures 3 and 4.From the figure, it can be seen that the maximum stress is 423 MPa, which occurs at the connection between the crossbeam and the support leg. The overall stress is relatively small, below 47 MPa; The maximum equivalent deformation is 1 mm, indicating that the steel structure size chosen for the support is unreasonable, resulting in excessive selection of safety factors for some components and insufficient strength for some components. Therefore, it is necessary to redesign the support component structure by changing the two cantilever ends to support legs, adding 4 support legs, increasing the size of the transverse beam, and reducing the size of the support legs.The analysis results obtained by recalculating are shown in Figures 5 and 6. From the figure, it can be seen that the maximum equivalent stress is 37.8 MPa, and the overall equivalent stress distribution is between 25.8 and 16.9 MPa, with very small equivalent deformation. The structural design and strength of the support arrangement meet the production and strength requirements, and the design is reasonable.
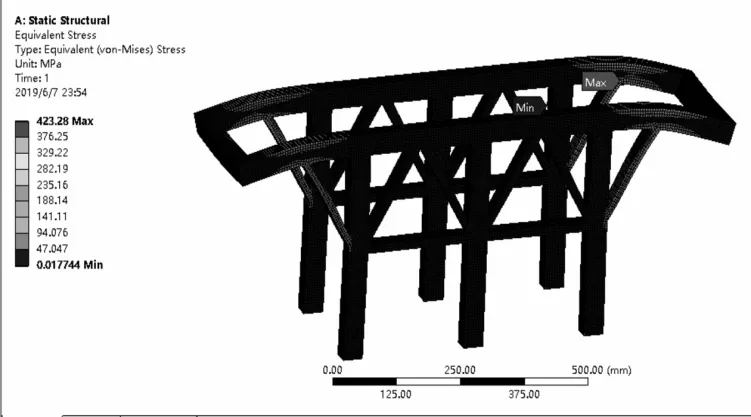
Figure 3 Cloud diagram of bracket equivalent force
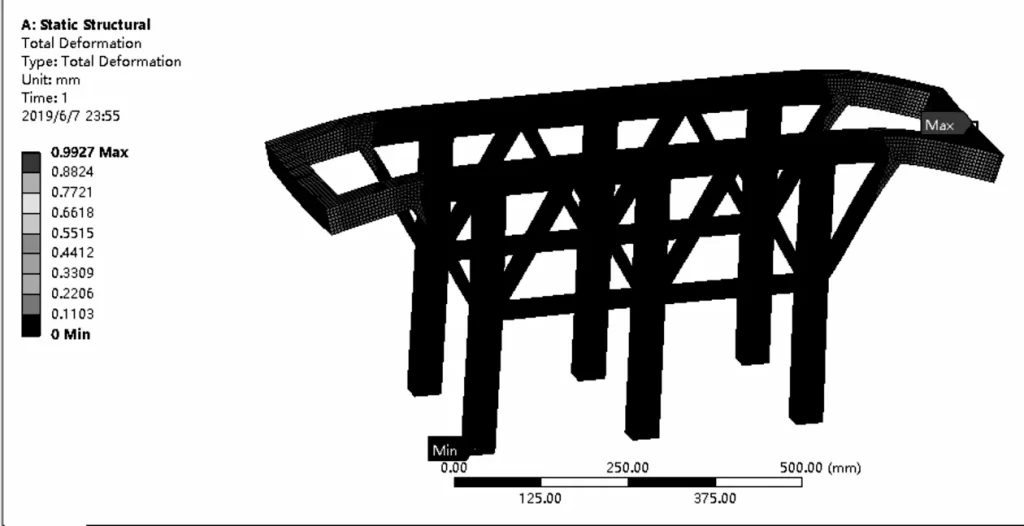
Figure 4 Equivalent deformation cloud map of bracket
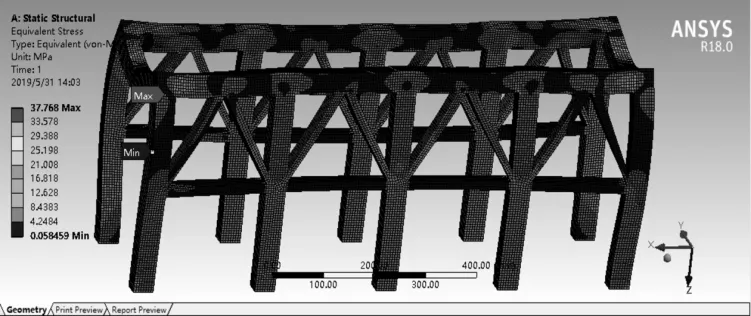
Figure 5 Equivalent stress cloud diagram of the overall support
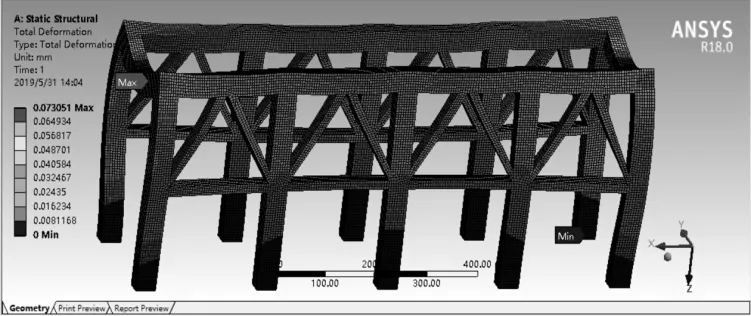
Figure 6 Cloud Chart of Equivalent Deformation of the Bracket as a Whole
3. Conclusion
SolidWorks 3D drawing software is used to model and design the structure of the hydraulic fully automatic brick making machine ingredient system. ANSYS software is used to verify and analyze its strength, and solutions are proposed based on existing problems. The design is improved to meet the design and usage requirements. The batching system, combined with working devices, has set up three production lines in a certain enterprise, achieving an annual output value of 360 million pieces of fly ash. The use of this equipment has achieved the benefits of waste utilization, energy conservation and environmental protection, and is directly promoted to other fields.