Abstract: Most domestic brick machine has some defects, for example, the anti -impact property is low, parts and components replacement are often needed. The working principal and structure of non-burned machine is studied. The power of non-burned brick is offerred by the hydraulic pump system. The design of hydraulic system can ensure the stability and efficiency of entire system. 3D model and assembly of non-kiln brick machine hydraulic pump station is carried out based on UG.
Key words: brick maker; hydraulic system; hydraulic pump system; 3D modeling
1. Structural composition of non firing brick making machine
The non burning brick making machine introduced in this article is a four column and four cylinder synchronous brick making machine. The upper and lower crossbeams are welded with high-quality steel plates, making it a high-quality equipment for producing large concrete products such as pavement bricks and curbs.
The execution mechanism of the non firing brick making machine mainly consists of the body structure, feeding mechanism, brick pressing mechanism, scraping mechanism, pallet mechanism, etc. It mainly completes the actions of loading, pressing bricks, unloading bricks, etc. In the design, it is required that the volume of each material bin should have adjustable functions to adapt to the requirements of different brick types. At the same time, it is required that the equipment has the advantages of high efficiency, strong resistance to high load of bricks, adjustable brick shape, compact structure, and environmental protection. The basic structure designed according to the above requirements is shown in Figure 1.
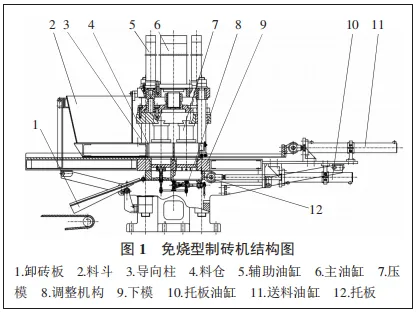
Figure 1
The working process of the brick making machine is as follows:
- The mixed industrial waste such as fly ash is transported by the conveyor belt to hopper 2. At this time, the pressing mold 7 stays at the highest position, and the material bin 4 in the feeding mechanism stops below hopper 2 to prepare for material collection. The feeding oil cylinder 11 pulls the hopper 4 directly below the pressing die 7, and the flat plate above the feeding mechanism blocks the hopper 2. The industrial waste from hopper 2 falls into the corresponding mold cavity of the lower die 9. Then, the feeding oil cylinder 11 causes the feeding mechanism to return to the bottom of hopper 2 to continue the next material collection.
- The main oil cylinder 6 and auxiliary oil cylinder 5 cause the compression mold 7 to press down along the guide column 3 into the mold cavity, and the elastic baffle in the mold cavity retracts into the support plate 12. Then the main oil cylinder 6 and auxiliary oil cylinder 5 cause the pressing die 7 to move upwards, and the supporting plate oil cylinder 10 drives the supporting plate 12 to move. The supporting plate 12 drags the unloading plate 1 to the right.
- The main oil cylinder 6 and auxiliary oil cylinder 5 cause the pressure mold 7 to descend and press the formed bricks onto the unloading plate 1. Then, they drive the main oil cylinder 6 and auxiliary oil cylinder 5 to raise the pressure mold 7 to the initial position. At the same time, they drive the supporting plate oil cylinder 10 to push the supporting plate 12 to the left of the unloading plate 1, and the bricks slide into the transmission belt.
If the corresponding die and cavity are replaced, different brick types can be pressed. By manually operating the adjustment mechanism 8 in Figure 1, bricks of different thicknesses can be pressed, thus achieving adjustability for different brick types and thicknesses.
2. Design of hydraulic system for brick making machine
2.1 Determination of Main Parameters of Hydraulic Cylinder
The working cycle of the unburned brick making machine is as follows: pallet extension → feeding pallet extension → feeding pallet return → rapid mold down → mold pause → pallet return → mold down → mold return. Calculate the working pressure, main structural dimensions, speed, time, and output force of the hydraulic cylinder based on the main parameters and performance requirements of the hydraulic system.
2.2 Proposed Basic Circuit
The hydraulic system is a high-pressure system, and the working cycle mainly consists of two stages: low-pressure large flow and high-pressure small flow. During rapid travel, the maximum flow rate is output, while during work, only the flow rate that matches the needs of the hydraulic cylinder is output. Therefore, choosing a swashplate axial piston pump is more reasonable.
According to the motion mode and requirements of the system, a differential connection motion loop is used to achieve rapid motion. During fast forward and fast reverse, the pump supplies oil and the hydraulic cylinder achieves differential connection.
Using a speed switching circuit with an electromagnetic valve to control the transition from fast forward to work forward. Compared with the stroke valve, the electro-hydraulic directional valve can be directly installed on the hydraulic station and controlled by PLC. The pipeline is simpler and the stroke size is also easy to adjust.
The system does not have strict requirements for directional stability, so a directional circuit with an electromagnetic directional valve is selected. To facilitate differential connection, both the support plate oil cylinder and the feeding oil cylinder are controlled by a three position four way electro-hydraulic directional valve.
2.3 Determine the schematic diagram of the hydraulic system
The schematic diagram of the hydraulic system can be determined based on the proposed basic circuit, as shown in Figure 2.
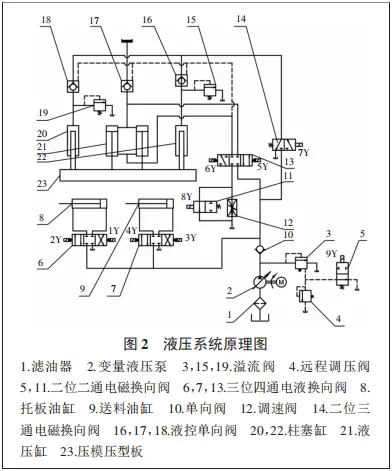
Figure 2
The oil source of the system is one-way variable displacement pump 2, and its pressure is set by relief valve 3, solenoid valve 5, and remote relief valve 4. Check valve 10 is used to prevent pressure oil from flowing back. The actuator of the system consists of a support plate oil cylinder 8, a feeding oil cylinder 9, a plunger cylinder 20, 22 for pressing the molded plate, and a hydraulic cylinder 21 (2).
The support plate oil cylinder 8 is controlled by a three position four way electro-hydraulic directional valve 6, the feeding oil cylinder 9 is controlled by a three position four way electro-hydraulic directional valve 7, the hydraulic cylinder 21 is controlled by a three position four way electro-hydraulic directional valve 13, a two position two way solenoid valve 11, a speed regulating valve 12, a hydraulic control one-way valve 17, and a solenoid valve 14, the plunger cylinder 20 is controlled by a hydraulic control one-way valve 18, an overflow valve 19, and a two position three way solenoid valve 14, and the plunger cylinder 22 is controlled by a hydraulic control one-way valve 16 and an overflow valve 15 Two position three way solenoid valve 14 controls. The strokes of the six hydraulic cylinders mentioned above are evenly distributed with varying numbers of stroke switches, which are used to send signals to the three-position four-way solenoid valve directional valve, as well as the two-position two way and two position three way solenoid valves [4,5], to achieve the predetermined action.
3. 3D modeling of hydraulic pump station for brick making machine
This hydraulic system adopts an integrated block type hydraulic station device. It consists of the following parts: oil tank, hydraulic pump device, bracket, integrated block component, external pipeline bracket, and PLC control box. Among them, the hydraulic pump device is installed on the oil tank, and the rest is installed on the bracket, which is then connected by the oil pipe joint according to the needs of the oil circuit.
After designing each component, it is also necessary to consider the convenience of valve components installation, adjustment and maintenance, as well as the neat and beautiful appearance. For example, there is a certain axial distance between the directional valves, which is convenient for manual adjustment or disassembly of the electromagnet. Install an external pipeline support at the outer edge of the support to facilitate the fixation of the external pipe, thereby increasing rigidity, neatness, and aesthetics; The pipes that move with the working parts are made of flexible pipes, which should avoid twisting during installation to avoid affecting their service life. Parallel pipes should be kept at a certain distance and fixed with pipe clamps.
Finally, after modeling the various components of the hydraulic system according to the requirements in UG software, the components are assembled according to the design requirements and assembly relationships of the hydraulic pump station system, forming a solid model of the hydraulic pump station as shown in Figure 3.
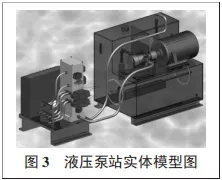
Figure 3
4. Conclusion
This design features a compact structure, strong impact resistance, and smooth operation for the new type of non burning brick making machine, achieving the expected design goals. If combined with PLC control technology, the hydraulic system can be more precise and flexible to complete the expected control tasks.