Home
Recommended products
BRICS Machinery Company – Your Trusted Partner in Construction Equipment
At BRICS Machinery Company, we take pride in offering an extensive range of high-quality machinery to cater to all your construction needs. Our diverse product lineup includes:Block Machine: Our state-of-the-art block machines are designed for precision and efficiency. Whether you need hollow, solid, or interlocking blocks, we have the right solution to meet your construction requirements.Brick Machine: We specialize in manufacturing brick machines that produce top-quality bricks, ensuring the success of your building projects.Block Making Machine: Our block making machines are engineered to create various types and sizes of blocks, providing you with flexibility and performance.Brick Making Machine: For durable and well-crafted bricks, our brick making machines are the answer. They are designed to produce bricks of exceptional quality.Concrete Block Making Machine: Experience the power of our concrete block making machines, built with advanced technology to produce strong and reliable concrete blocks.Interlocking Brick Machine: We offer interlocking brick machines that simplify the construction process, creating robust interlocking bricks for your projects.AAC Machinery: As a leader in the industry, our AAC machinery is tailored to produce high-quality Autoclaved Aerated Concrete (AAC) blocks, known for their lightweight and insulation properties.AAC Block Machinery: Our AAC block machinery is a testament to innovation and sustainability, making the production of AAC blocks efficient and eco-friendly.ALC Panel Machinery: If you’re looking for machinery to manufacture Autoclaved Lightweight Concrete (ALC) panels, our ALC panel machinery is designed for modern building systems.
main product videos
The motor for the host machine is Germany SIEMENS brand or ABB brand.Control PLC: we select original Japan Mitsubishi PLCcombine with independently develop machine control program, assure stable and high efficiency working status.The Travel switche will use France Schneider brand and Japan Omron.Mould: newest heat treatment device and carburizing treatment will assure longer mould life span and ensure the strength of mould reach to 54-58 HRC so that the mould can be used more than 100 thousand times.Material and welding: all materials and spare parts selected according to international CE standard, Carbon dioxide protection welding will assure whole line stable running.
Main Features: Can produce differernt kinds of hollow blocks, solid blocks.Have passed Europe CE and ISO9001 standard.Use the heat treated mould,so the useful life of the mould is more longer.Suitable for small investment
As the advanced hydraulic ratio control technology is adopted so that the oil pressure of each branch of the circuit can be controled at will and various bricks with the same high quality can be produced using different raw materials.
PLC intelligent control system which equiped with data input and output device,advanced safety logic and fault self-diagnosis system is adopted in full of the production procedure.
Full automatic block paver brick block making machine can produce various solid blocks , hollow blocks, pavers and curbstones by changing moulds.
Full automatic block paver brick block making machine adopt to hydraulic pressure moulding system , so the brick machine has more stable and higher-efficiency working status and the bricks produced are of better quality, larger density and higher strength.
Precise line cutting technology and carburizing treatment technology to prolong mould life and increase precision of the block.
Switches will use Japan Omron or France Schneider band, motor will use Siemens or ABB brand.
Features & Advantages of QT12-15 fully automatic block making machine line:Full automatic and hydraulic automatic block making machine , can produce all kinds of bricks, and just change the moulds, such as the solid bricks, hollow blocks, paver blocks and so on.German Siemens motors.Japan Mitsubishi PLC.Omron travel switch.The moulds: We adopt the heat treatment technique to increase the lifespan of the moulds.Certificates: SGS/CE/ISO9001 2008.Mould heat treatment & carburization technology.Strong High-Strength Steel Structure
Main product catalogs
production workshop
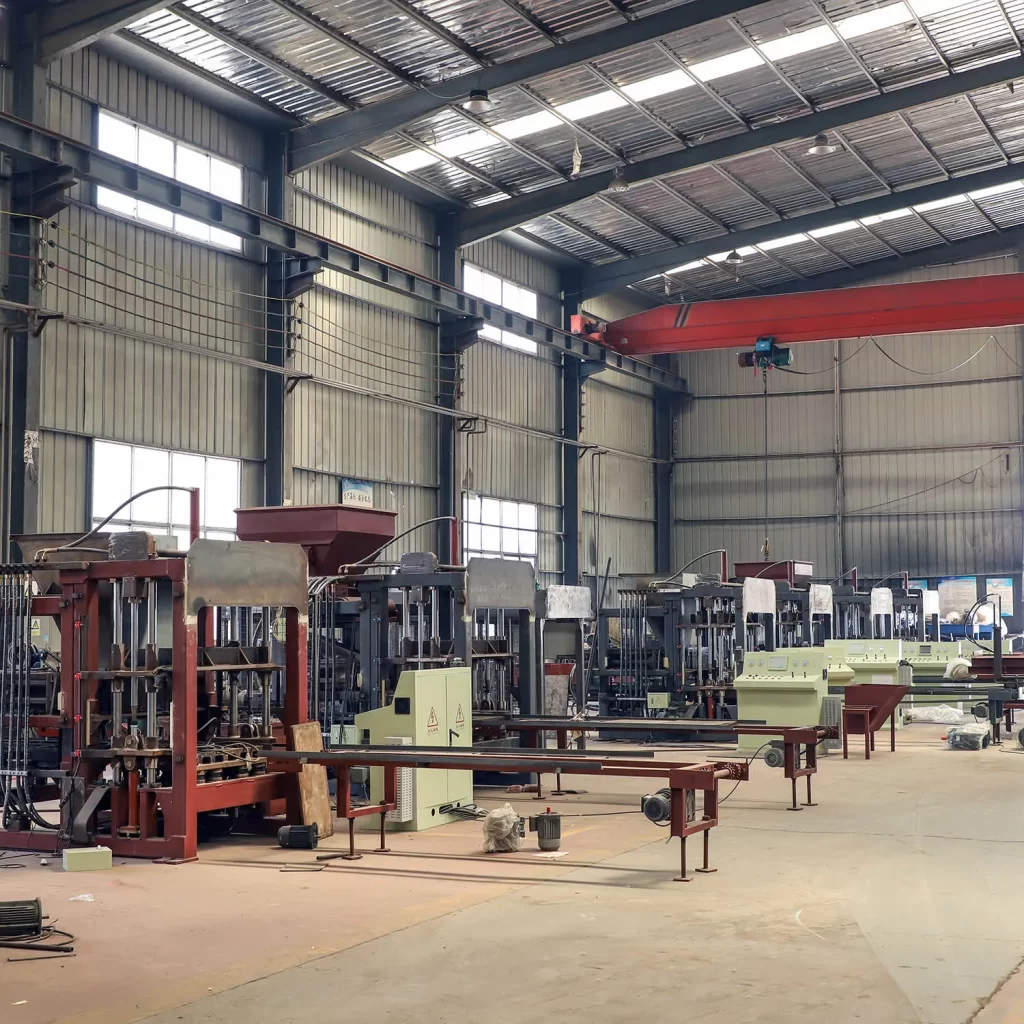


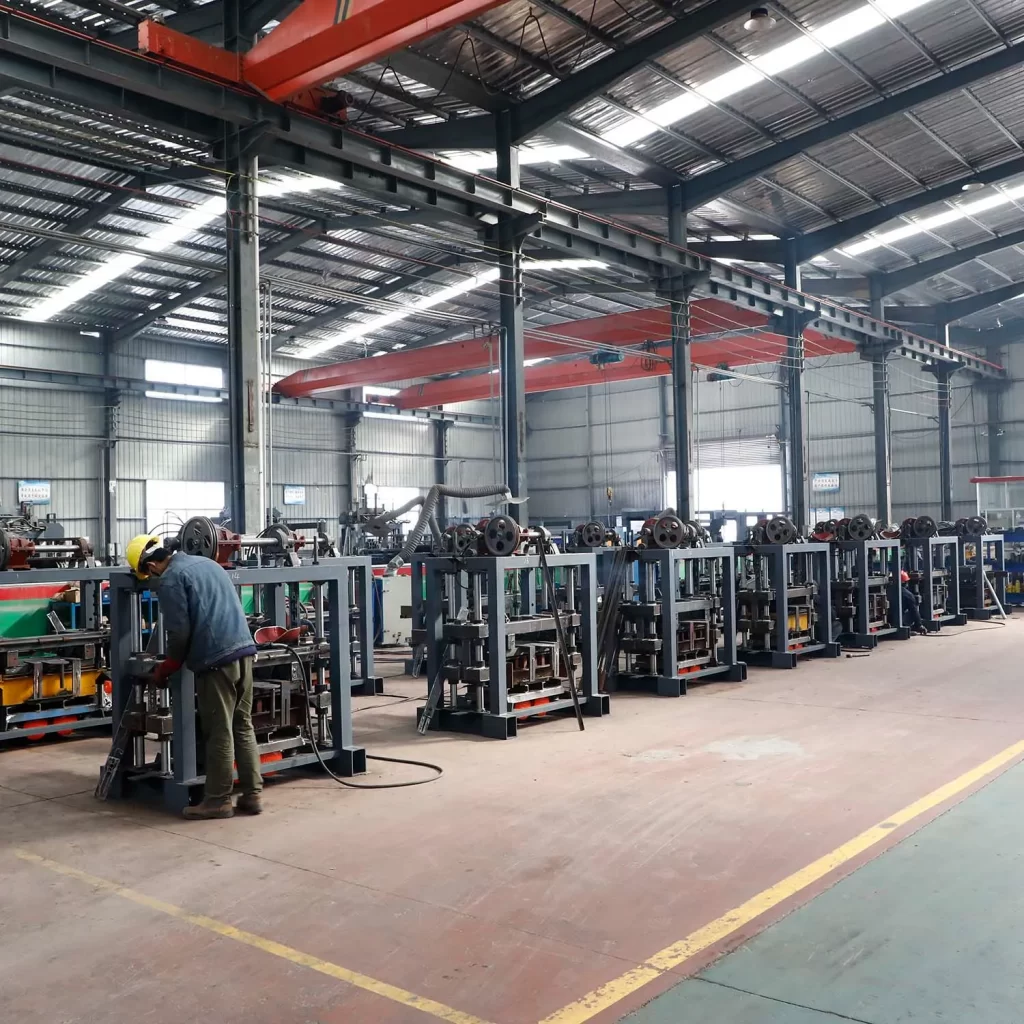
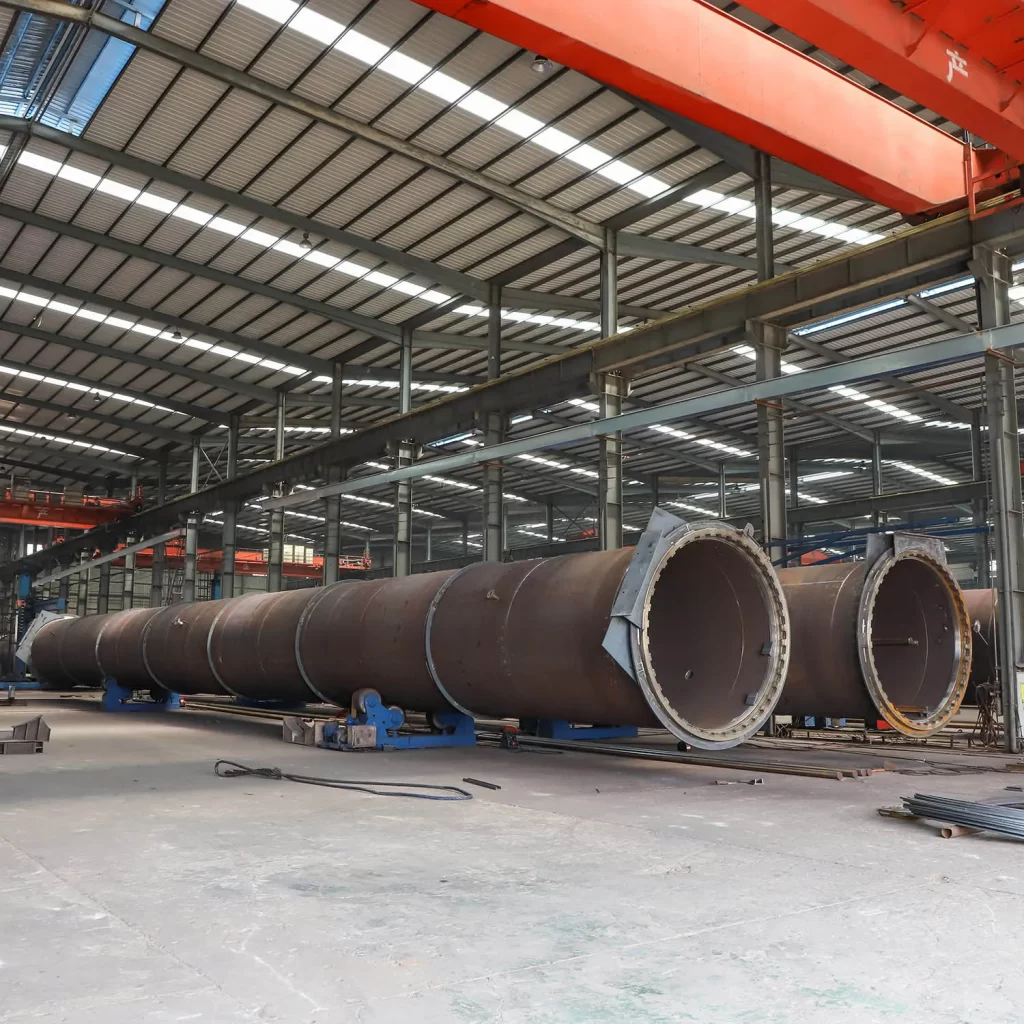
Technological Development
The company is part of Shandong Province’s high-tech industry and has established a provincial-level enterprise technology center and the Shandong Province Construction and Building Materials Machinery Engineering Laboratory. The company has a dedicated technology department and has engaged in technical cooperation with the China Academy of Building Research and Germany’s Katzbeck Group. To date, the company and its subsidiaries hold three invention patents and multiple utility model patents.
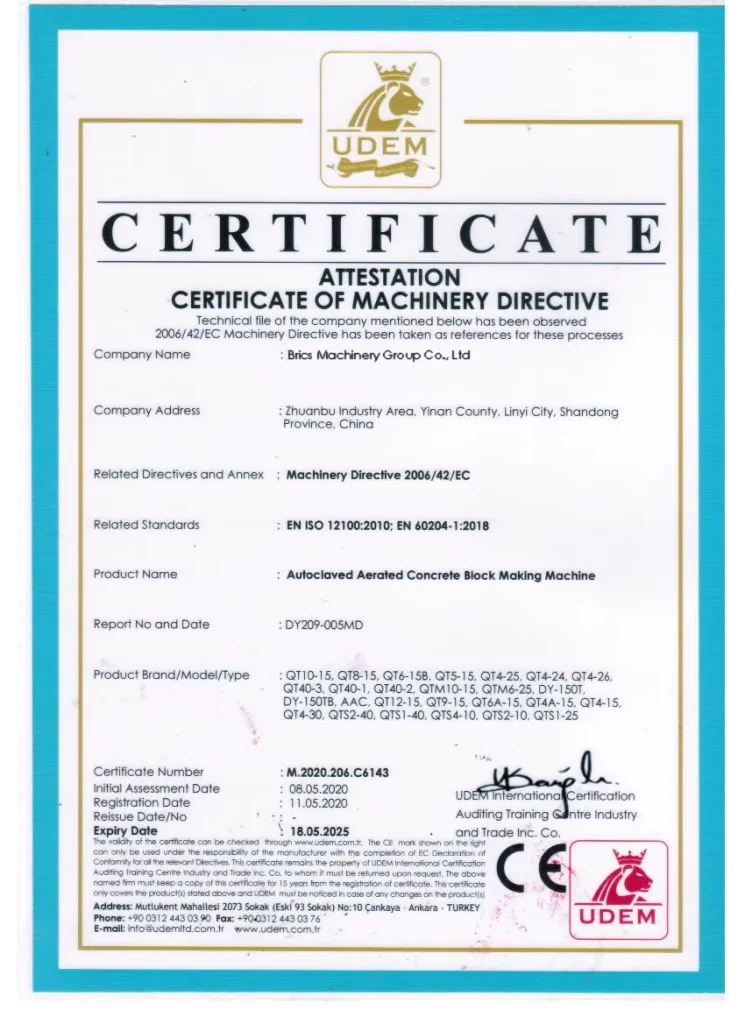
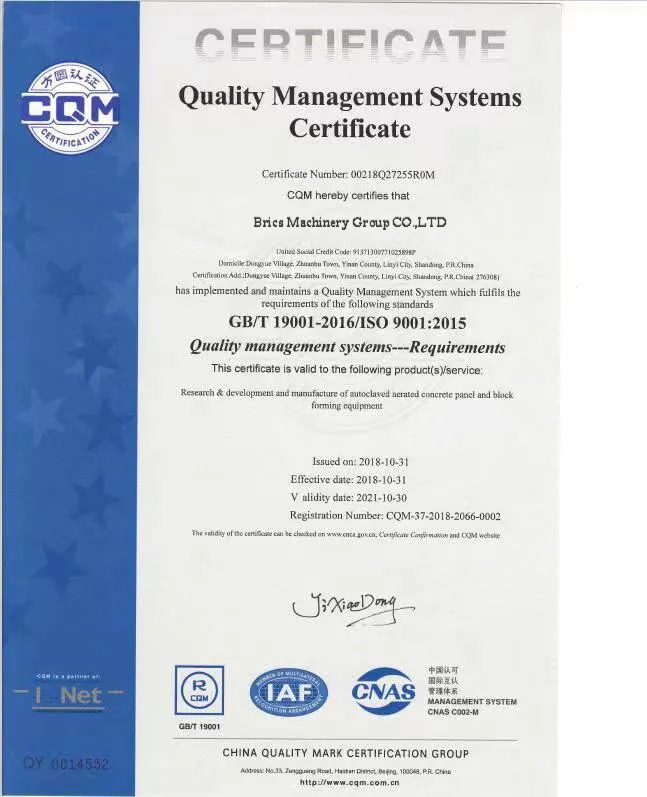
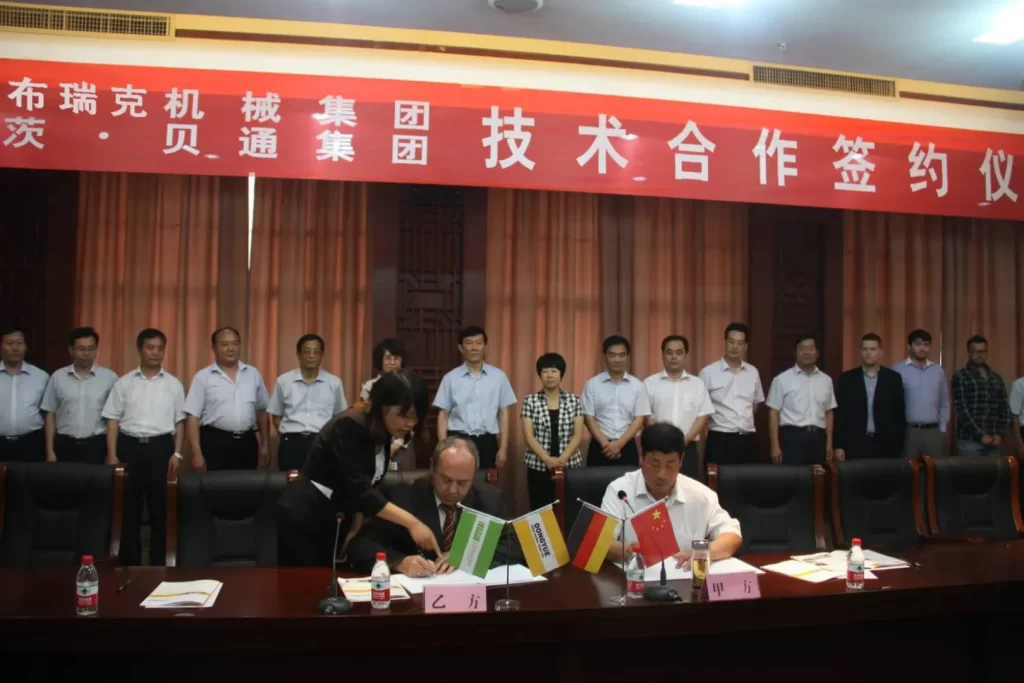
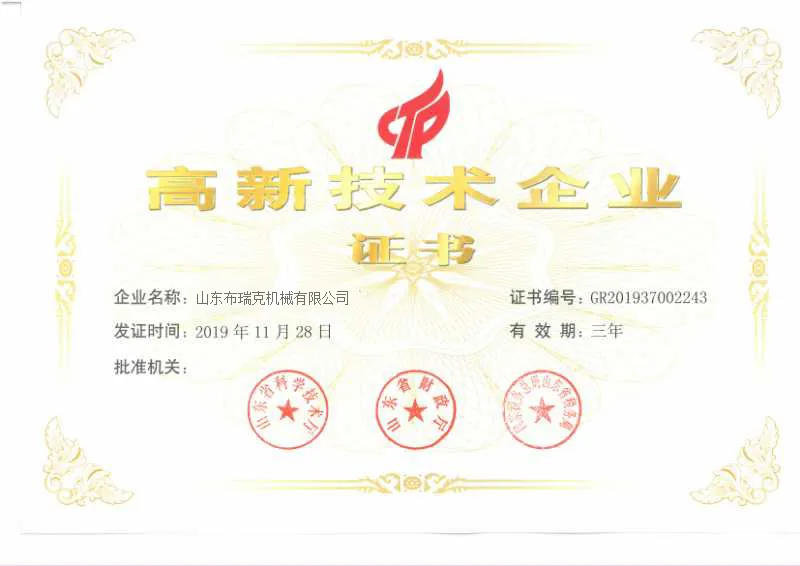
client feedback
Customer Communication at the Canton Fair
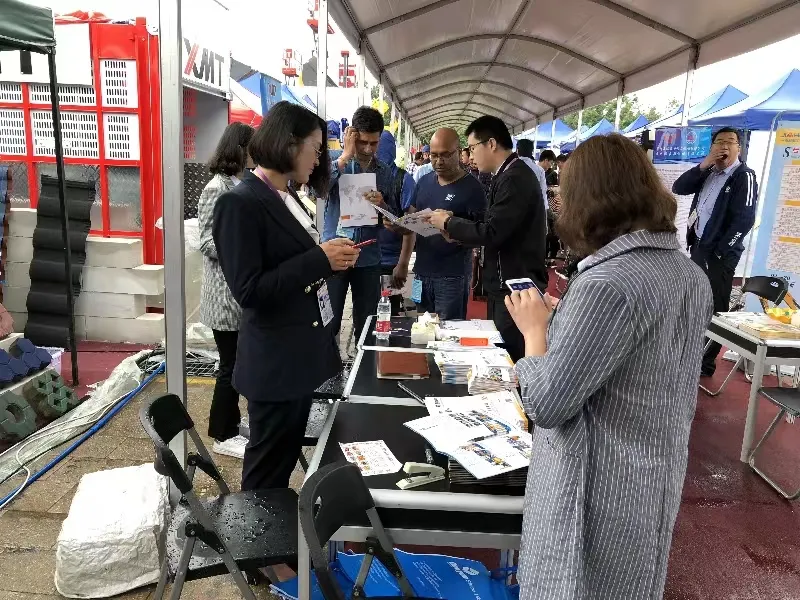



Why do customers choose us?
The advantages of using two side buckle plates above the brick making machine , Machine reliability design Increase stability: The buckle type structure on both sides can provide better stability, especially during high-speed operation. It can reduce vibration and vibration, making the operation of the brick making machine more stable and controllable, and helping to produce high-quality bricks.Reduced maintenance: The two side buckle design is usually more durable than other designs because it can reduce wear and damage. This reduces maintenance costs and extends the lifespan of the equipment. There are also some other benefits.The use of vibration motors in brick making machines has many benefits, including:Improving compaction effect: Vibration motors can generate vibrations or vibrations, effectively helping to compact bricks or other building materials. This vibration can make the material more evenly distributed within the mold and fill it more tightly, thereby improving the compaction effect. This leads to higher quality and more uniform bricks.Improving production efficiency: Vibration motors can accelerate the production speed of bricks. It can promote the smooth flow of materials, help fill molds with materials and quickly compact them, thereby reducing the production time of each brick and improving production efficiency. There are also some other benefits.
The use of two oil cylinders in a brick making machine has the following benefits:Increase stability: The collaborative work of two oil cylinders can improve operational stability. They can coordinate with each other to reduce vibration and instability, making the operation of the brick making machine more stable and controllable. This is particularly important for tasks that require high-precision operations.Reduce maintenance costs: Two oil cylinders share the workload, and each cylinder has a smaller load. This reduces the risk of wear and damage to each cylinder, prolongs the lifespan of the equipment, and thus reduces maintenance and repair costs.In summary, using a brick making machine with two oilcylinders can improve operational stability, production efficiency, product quality, reduce maintenance costs, and provide greater production flexibility, all of which are very beneficial to the brick making industry.
We have adopted high-quality accessories to ensure the excellent performance and long-term reliability of the brick making machine. Unlike other manufacturers, we do not compromise on quality and prefer to choose accessories that are slightly higher in cost, as we are well aware that such investments will generate huge returns in long-term operation. This commitment indicates that we attach great importance to customer reliability and product quality, not only reducing maintenance costs, but also ensuring that every brick produced by customers is of high quality. We are committed to providing excellent solutions that exceed market expectations.
Design of brick making machine to improve production efficiency,A brick making machine with front and rear separation is a device used to manufacture bricks, which divides the brick making process into two main parts: front-end molding and back-end sintering. In the front-end molding section, the raw materials are mixed, compressed, and formed into the shape of bricks. Subsequently, these newly made bricks are sent to the backend sintering section for sintering or hardening at high temperatures to improve the strength and durability of the bricks. The brick making machine with front and rear separation improves production efficiency, ensures the consistency of bricks, reduces energy consumption, and is widely used in the construction and brick manufacturing industries.
In the Egyptian region, the quality requirements for brick-making machines typically include:
- Production Efficiency: Brick-making machines need to have high production efficiency to meet the demands of construction and infrastructure projects. Rapid brick production can help reduce construction costs and accelerate project timelines.
- Brick Quality: The bricks produced by brick-making machines must conform to international or local quality standards. This includes the dimensions, strength, durability, and appearance of the bricks. High-quality bricks are crucial for the stability of building structures.
Modern brick making machines are equipped with sophisticated electrical systems. These systems typically include control panels, sensors, and motors. The control panel serves as the brain of the machine, allowing operators to set various parameters, such as brick size, density, and production speed. Sensors are used to monitor critical aspects of the process, ensuring the machine operates within safe and efficient limits. Electric motors drive the conveyor belts, mixing components, and other essential parts of the machine.The hydraulic system in a brick making machine is responsible for applying the necessary force to compress and shape the raw materials into bricks. It typically includes hydraulic pumps, cylinders, and valves. Hydraulic power is harnessed to press the material into a desired shape within the mold, resulting in consistent and well-structured bricks. The ability to finely control hydraulic pressure and timing is a game-changer in brick production.
The use of solid shafts on the side of brick making machines has the following benefits:Increased stability: The solid shaft provides higher stability, reduces vibration and shaking, and helps ensure smoother operation of the brick making machine.Improved durability: Solid shafts made of sturdy materials have a longer service life, reducing maintenance and replacement costs.High quality brick production: The stability and reliability of the solid shaft help ensure that the size and shape of each brick are consistent, thereby improving the quality of the bricks.Improved operational efficiency: The solid shaft transmits power and motion to various components of the brick making machine, ensuring smooth transportation and effective molding of raw materials, thereby improving production efficiency.In summary, using a solid shaft brick making machine improves stability, durability, and operational efficiency while producing high-quality bricks, making it an excellent choice for the brick manufacturing industry.